~ What is CNC turning? ~
The CNC turning process is used to produce certain part types. It is a specific area of CNC Machining, referring to the subtractive machining process where the final workpiece or material is spun at a high speed. During this high speed turning, the cutting tool shaves away the material until the part is completed to a satisfactory shape and size. CNC turning utilises one of the oldest forms of manufacturing, with turning used as far back as ancient Egypt. With this guide, we’ll look at when this is necessary and how it functions
What is CNC?
CNC (Computer Numerical Control) is the broader term for the manufacturing process that is led by a computer programme. The parts are designed and developed using CAD (Computer-Aided Design), and this is then used to control the CNC turning machine to produce the part accurately, with the cutting tools following the long lines of code to produce precise and small cutting tool movements.
What is turning as a process?
CNC turning is a process where materials are held in a chuck and rotated at speed as a tool is fed to the piece to remove material to create the required shape and size. A turret has tools attached to it and is programmed to move the material and remove parts of it as designated in the attached programme. This is also referred to as subtraction machining, as it is where material is removed to create the finished part rather than adding new material. It is different to other types of cutting processes where the tools move and spin, rather than the material being worked on.
The difference between a traditional lathe and the machines that are used for turning manufacturing today is that the modern machines are numerically controlled. If there is a desire for complex and very precise shapes and designs, the entire process can become faster and more precise when using modern machines, as there is no need to keep stopping and starting and to keep a constant eye on supervising the process and adjusting the tools and materials where necessary.
What is needed to make a CNC turned part?
To put it simple, there are three things you need to make the completed turned part through CNC turning:
The design of the piece
This is where the design of the finished piece is translated into the CNC turning machine language in a saved CAD file.
Cutting speed and feed rate
These are the two variables to understand. The turning speed is the velocity at which the workpiece rotates, and the feed rate is the velocity at which the cutting tool moves along the rotating workpiece.
The raw material
The type of material used will determine the properties of the resulting part, with different potential smoothness on the finished surface, and different functionality depending on the raw material used. The size, shape, and weight will also have an impact on the turning process.
Are there different shapes that can be made with CNC turning?
The versatility of CNC turning machining is one of its biggest benefits. Although most commonly, this type of manufacturing is used to work on cylindrical shapes, cones, and disks it also offers exceptional capabilities for raw materials that are square or hexagonal in shape. In fact, there are a wide range of profiles that are available to work on efficiently, with the functionality of a lathe and turning centre allowing for turning that is straight, tapered, threading, external grooving, boring, drilling, or knurling. The workpiece is held in place by a chuck, which spins at varying RPMs (rotations per minute) for the desired impact and effect.
The benefits of CNC turning
As we have already noted, there are a few benefits to CNC turning to create parts. It offers speed and precision, along with flexibility and versatility in parts and shapes that can be worked on. If you need cylindrical or symmetrical parts to be created fast, repeated consistently at a high volume of production, it certainly brings major benefits. You can also see that it is capable of other things too, such as drilling, boring, taper turning, and reaming. Parts are created to a high standard and with an incredibly smooth finish.
Is CNC turning the right choice for this part?
CNC turning is one of the most important methods in manufacturing, developed from one of the most ancient and traditional forms of manufacturing dating back centuries. If you are unsure as to whether the part you need to produce would benefit from CNC turning, there are a few things to consider.
The design considerations are:
The geometry of the parts
As seen above, the different shapes and geometry that CNC turning is capable of provides some flexibility in what you can achieve. If your part is cylindrical or symmetrical in particular, CNC turning is a great choice. This commonly includes parts such as gears, pullers, and shafts. If there is a complex 3d geometry required where there is a need for more complex rotational movements, CNC milling, injection moulding or 3D printing might be a better options.
The materials used
The compatibility with turning will also depend on the materials being used. This process is suited best with materials that are easy to machine, such as brass, plastics, and aluminium. Hard and abrasive materials such as titanium and stainless stell are often better worked on with a specialist tool.
The tolerance required
CNC turning can lead to tight tolerances and deliver the highest levels of precision to +/-0.001 inches (0,025mm), depending on the machine and the materials used. If tighter tolerances are required, you may be better looking at alternative manufacturing or secondary processes such as polishing and grinding to get to the desired end product.
If these considerations match the part you are looking to produce, CNC turning is the correct choice for you.
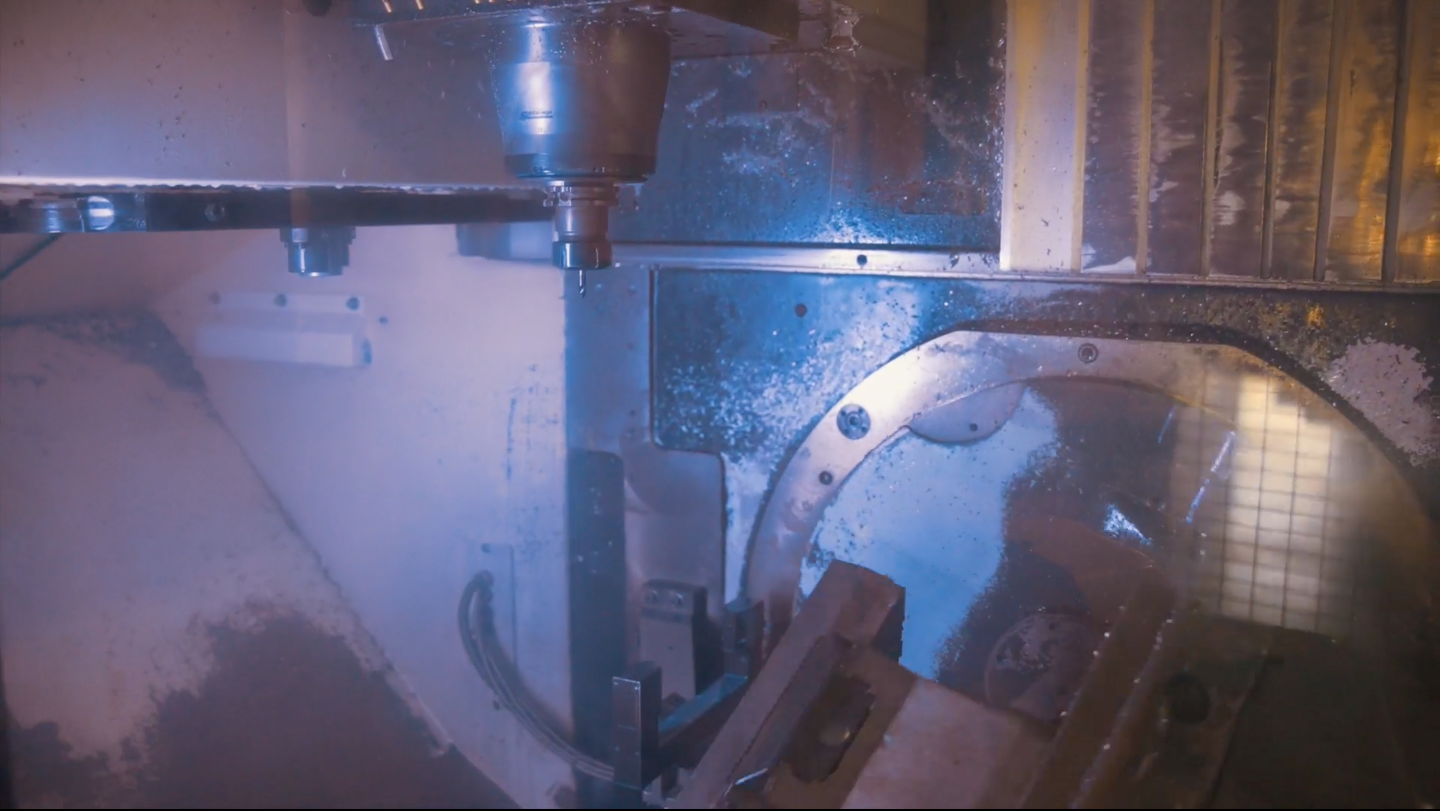
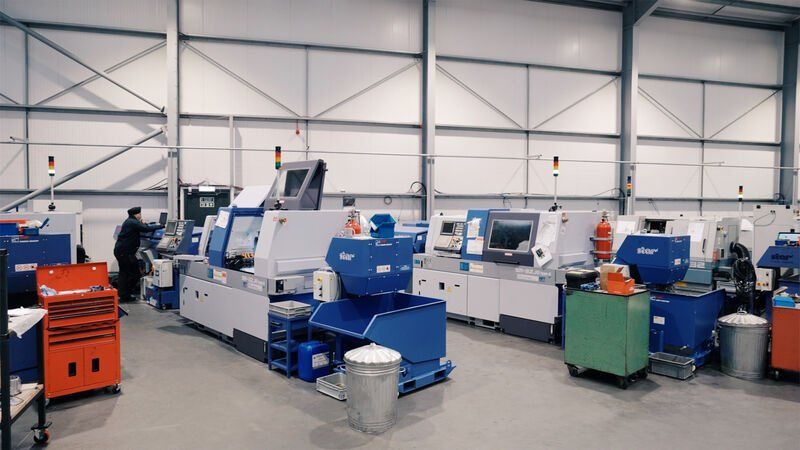
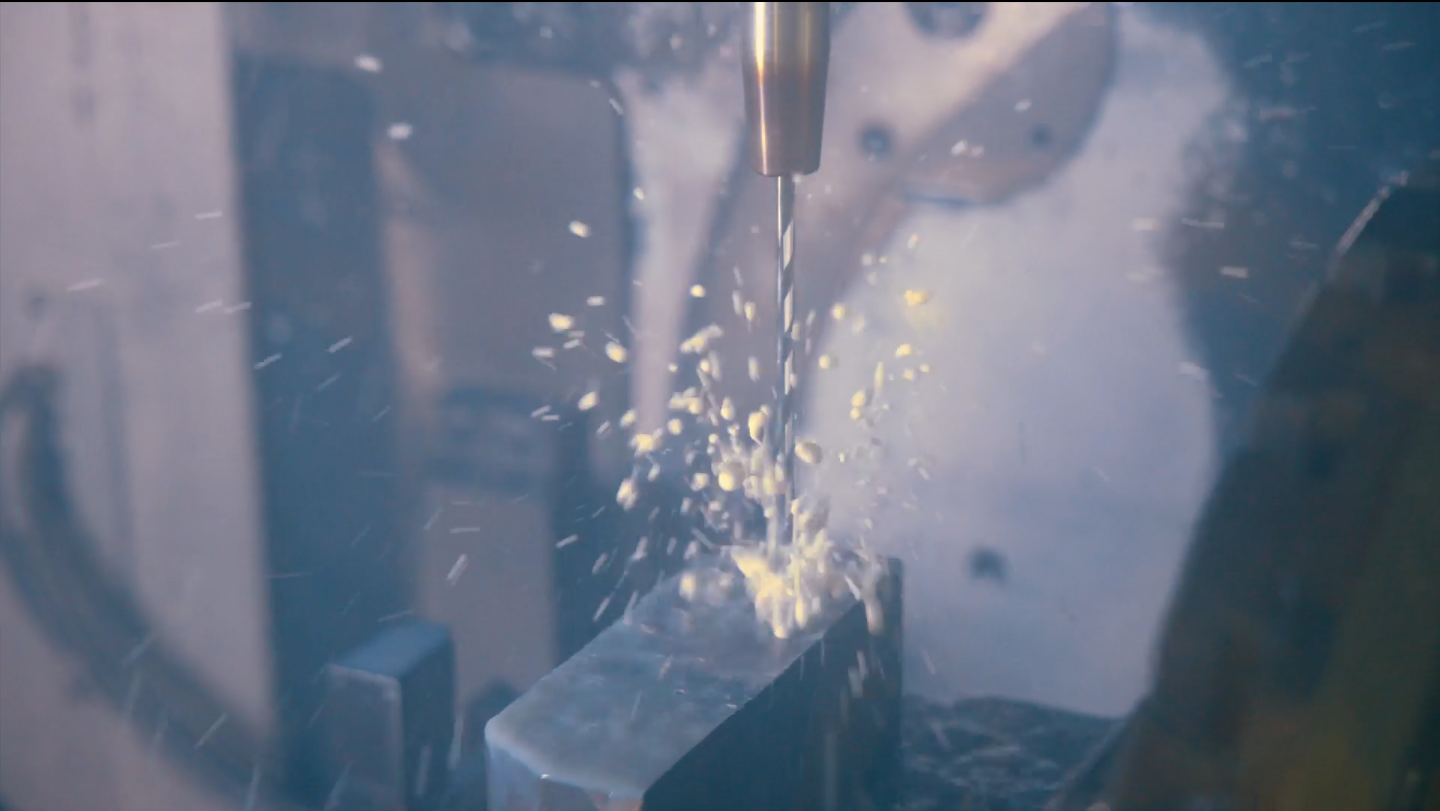
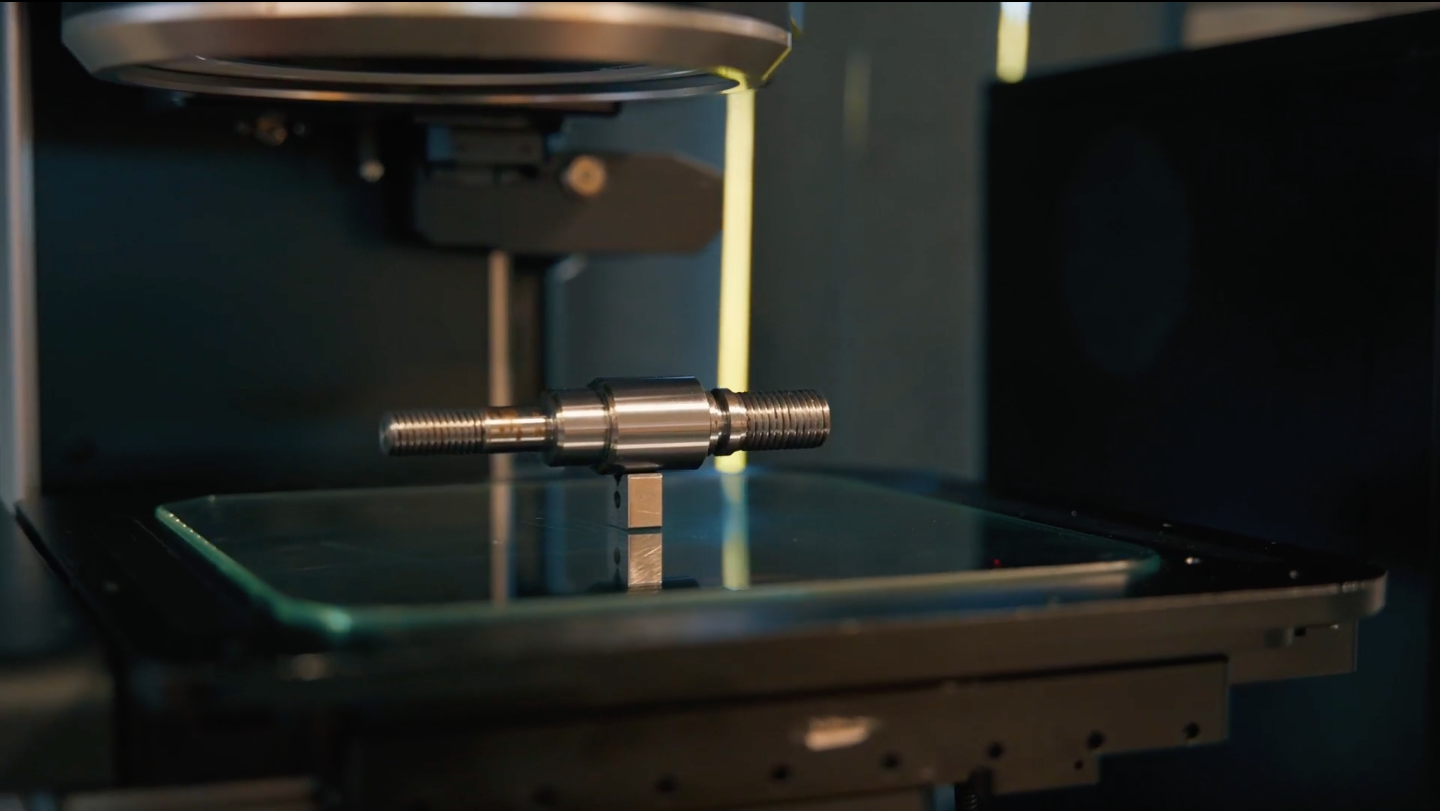