~ Exploring the Variety of Materials Used in CNC Machining ~
The choice of materials influences the outcome of the machining process, so it's important to know about all the options.
When it comes to precision engineering and CNC machining, the selection of materials is a decision that significantly impacts the final product's quality, performance, and cost-effectiveness. With that being said, each material presents its own set of challenges and opportunities, impacting the way components are designed, manufactured, and utilised across various industries.
If you are a manufacturing professional who is interested in learning about the possibilities when it comes to
CNC machining materials, you have come to the right page! In this article, we have explored the diverse range of materials used in CNC machining, along with their real-life applications. But first, let's understand the challenges and considerations to keep in mind when identifying the right type of material for your project.
Challenges and Considerations in Material Selection
Factors Influencing Material Choice
Material selection in CNC machining is influenced by various factors, including mechanical properties, chemical compatibility, environmental conditions, and cost considerations. Balancing performance requirements with manufacturability and sustainability goals is essential for identifying the most suitable material for a given application.
Machinability and Tool Wear
Each material exhibits unique machinability characteristics, affecting tool life, cutting forces, and surface integrity during CNC machining. Optimising cutting parameters, tool selection, and coolant strategies is crucial for maximising productivity and minimising tool wear in diverse machining operations.
Cost and Availability
The cost and availability of materials play a significant role in manufacturing economics and supply chain management. Factors such as raw material prices, market demand, and geopolitical factors can impact material costs and availability, necessitating strategic sourcing and inventory management practices to mitigate risks and ensure uninterrupted production in CNC machining operations.
Materials Used in CNC Machining
In the early days of CNC machining, materials such as steel, aluminium, and brass were commonly used. These metals provided the necessary strength and machinability required for various applications. However, as technology advanced, so did the range of materials available for machining. Innovations in metallurgy and material science led to the development of specialised alloys and composites, expanding the possibilities for CNC machining.
Commonly Used Metals in CNC Machining
Aluminium Alloys
Aluminium alloys are known for their lightweight nature, corrosion resistance, and excellent machinability. Commonly used in aerospace, automotive, and electronics industries, aluminium alloys offer versatility and cost-effectiveness in CNC machining applications.
Stainless Steel
Stainless steel is renowned for its durability, corrosion resistance, and aesthetic appeal. Widely used in industries such as healthcare, food processing, and architecture, stainless steel requires specific machining techniques due to its hardness.
Titanium Alloys
Titanium alloys are valued for their exceptional strength-to-weight ratio, biocompatibility, and resistance to corrosion. Aerospace, medical, and marine industries utilise titanium alloys for components subjected to extreme conditions. However, titanium's high strength and low thermal conductivity present challenges in CNC machining, requiring specialised tooling and cutting strategies.
Brass and Copper Alloys
Brass and copper alloys are renowned for their conductivity, malleability, and aesthetic appeal. Commonly used in electrical and plumbing applications, these materials offer excellent machinability and surface finish characteristics in CNC machining processes.
Carbon Steels
Carbon steels are known for their strength, toughness, and affordability. Used extensively in construction, automotive, and machinery industries, carbon steels require careful consideration of machining parameters to avoid tool wear and achieve desired surface finishes.
Tool Steels
Tool steels are specifically designed for use in cutting tools and moulds, offering high hardness, wear resistance, and thermal stability. Used in CNC machining for precision cutting and forming operations, tool steels require specialised machining techniques to maintain dimensional accuracy and tool life.
These commonly used metals form the backbone of CNC machining, each offering unique properties and challenges that must be carefully considered during material selection and machining processes.
Engineering Plastics and Polymers in CNC Machining
Engineering plastics and polymers encompass a wide range of materials used for their lightweight, corrosion resistance, and versatility. Common examples include ABS, acrylic, nylon, and PEEK. Unlike metals, plastics require different machining techniques due to their lower melting points and tendency to deform under heat and pressure.
Types of Engineering Plastics Used
Engineering plastics are chosen based on specific application requirements. For instance, ABS is commonly used in automotive components due to its impact resistance and affordability, while PEEK is favoured in aerospace and medical industries for its high temperature resistance and biocompatibility.
Applications and Considerations
Engineering plastics find applications in diverse industries, including automotive, electronics, healthcare, and consumer goods. CNC machining of plastics requires careful consideration of cutting speeds, feed rates, and tool geometry to minimise heat generation and achieve precise dimensional accuracy.
Composite Materials in CNC Machining
Composite materials consist of two or more constituent materials with distinct properties, combined to create a material with enhanced mechanical, thermal, or electrical properties. Common types include fibre-reinforced composites, such as carbon fibre, fiberglass, and aramid fibre.
Fibre-Reinforced Composites
Fibre-reinforced composites offer exceptional strength-to-weight ratio, stiffness, and fatigue resistance compared to traditional materials. They find applications in aerospace, automotive, sporting goods, and renewable energy industries, where lightweight and high-performance components are crucial.
Composite Machining Techniques
CNC machining of composites requires specialised tooling and cutting strategies to accommodate the abrasive nature of fibres and prevent delamination. Techniques such as diamond-coated tools, low cutting speeds, and high-pressure coolant are used to achieve precise cuts and superior surface finishes.
Benefits and Challenges
Composite materials offer significant benefits in terms of weight reduction, improved performance, and design flexibility. However, challenges such as fibre orientation, tool wear, and material delamination must be carefully addressed during CNC machining to ensure optimal results.
Specialised Materials and Exotic Alloys
High-Temperature Alloys
High-temperature alloys, such as Inconel and Hastelloy, are designed to withstand extreme temperatures and corrosive environments. Widely used in aerospace, power generation, and chemical processing industries, these alloys pose challenges in CNC machining due to their high strength and heat resistance.
Super Alloys
Super alloys, including nickel-based and cobalt-based alloys, offer exceptional mechanical properties at elevated temperatures. Utilised in gas turbines, jet engines, and nuclear reactors, super alloys demand advanced machining techniques to overcome their hardness.
Exotic Materials Used in Aerospace and Defence
Aerospace and defence industries often require materials with unique properties, such as beryllium, tantalum, and titanium aluminides. These exotic materials offer superior strength, thermal stability, and corrosion resistance, albeit at higher costs and machining complexities. CNC machining of such materials demands expertise and precision to meet stringent quality and performance requirements.
Real-World Applications of Commonly Used CNC Machining Materials
Automotive Industry
In the automotive industry, CNC machining is utilised for the production of engine components, chassis parts, and interior fittings.
CNC machining materials such as aluminium alloys and carbon fibre composites are commonly machined to meet stringent performance and safety standards, enabling lightweight construction and fuel efficiency in modern vehicles.
Aerospace and Defence
Aerospace and defence sectors demand precision-engineered components with uncompromising reliability and performance. CNC machining of exotic materials like titanium alloys and superalloys is essential for fabricating aircraft structures, turbine blades, and missile components, ensuring optimal strength-to-weight ratio and resistance to extreme environments.
Medical Device Manufacturing
Medical device manufacturing requires precision machining of biocompatible materials such as stainless steel, titanium, and medical-grade polymers. CNC machining enables the production of intricate implants, surgical instruments, and prosthetic devices with exceptional dimensional accuracy and surface finish, contributing to advancements in healthcare and patient care.
Electronics and Semiconductor Manufacturing
In the electronics industry, CNC machining is instrumental in producing precision components for consumer electronics, telecommunications equipment, and semiconductor devices. From heat sinks and connectors to microelectronic packages and wafer handling equipment, CNC machining enables the fabrication of intricate parts with tight tolerances and high reliability. Materials such as aluminium alloys and engineering plastics are commonly used for electronic enclosures and PCB assemblies, ensuring optimal performance and durability in demanding electronic applications.
Renewable Energy and Green Technology
With the growing emphasis on renewable energy sources and sustainability, CNC machining plays a vital role in the production of components for wind turbines, solar panels, and energy storage systems. Precision-engineered parts such as gearbox housings, blade mounts, and battery enclosures require CNC machining to meet stringent performance requirements and ensure operational efficiency. Additionally, CNC machining enables the fabrication of lightweight and aerodynamic components for electric vehicles, advancing the adoption of green transportation technologies and reducing carbon emissions.
Precision Optics and Photonics
In the field of precision optics and photonics, CNC machining is essential for manufacturing lenses, mirrors, and optical mounts with sub-micron accuracy. From telescopes and microscopes to laser systems and fibre optic components, CNC machining enables the production of optical assemblies that meet the exacting demands of scientific research, telecommunications, and aerospace applications. Materials such as optical glasses, crystals, and specialised ceramics are carefully machined to achieve precise optical surfaces and geometries, facilitating the propagation and manipulation of light in diverse optical systems.
Emerging Trends and Future Prospects
Additive Manufacturing and 3D Printing Materials
The advent of additive manufacturing, or 3D printing, has revolutionised the production of complex geometries and customised components. Additive manufacturing materials range from thermoplastics and photopolymers to metal powders and ceramics, offering unprecedented design freedom and rapid prototyping capabilities. As additive manufacturing technologies continue to advance, new materials with enhanced properties and functionalities are constantly being developed, opening up exciting possibilities for CNC machining.
Sustainable and Eco-Friendly Materials
With increasing environmental concerns, there is a growing emphasis on sustainable and eco-friendly materials in CNC machining. Bio-based polymers, recycled metals, and biodegradable composites are gaining traction as viable alternatives to traditional materials, offering reduced carbon footprint and environmental impact. As sustainability becomes a key driver in material selection, manufacturers are exploring innovative solutions to minimise waste and resource consumption in CNC machining processes.
Nanomaterials and Microscale Machining
Nanomaterials, such as carbon nanotubes and graphene, exhibit extraordinary mechanical, electrical, and thermal properties at the nanoscale. These materials hold immense potential for applications in electronics, healthcare, and energy storage, driving research efforts towards scalable manufacturing processes and precision machining techniques at the micro and nanoscale.
Electronics and Semiconductor Manufacturing
In the electronics industry, CNC machining is instrumental in producing precision components for consumer electronics, telecommunications equipment, and semiconductor devices. From heat sinks and connectors to microelectronic packages and wafer handling equipment, CNC machining enables the fabrication of intricate parts with tight tolerances and high reliability. Materials such as aluminium alloys and engineering plastics are commonly used for electronic enclosures and PCB assemblies, ensuring optimal performance and durability in demanding electronic applications.
Renewable Energy and Green Technology
With the growing emphasis on renewable energy sources and sustainability, CNC machining plays an important role in the production of components for wind turbines, solar panels, and energy storage systems. Precision-engineered parts such as gearbox housings, blade mounts, and battery enclosures require CNC machining to meet stringent performance requirements and ensure operational efficiency. Additionally, CNC machining enables the fabrication of lightweight and aerodynamic components for electric vehicles, advancing the adoption of green transportation technologies and reducing carbon emissions.
Precision Optics and Photonics
In the field of precision optics and photonics, CNC machining is essential for manufacturing lenses, mirrors, and optical mounts with sub-micron accuracy. From telescopes and microscopes to laser systems and fibre optic components, CNC machining enables the production of optical assemblies that meet the exacting demands of scientific research, telecommunications, and aerospace applications. Materials such as optical glasses, crystals, and specialised ceramics are carefully machined to achieve precise optical surfaces and geometries, facilitating the propagation and manipulation of light in diverse optical systems.
In need of precision engineering and manufacturing solutions that push the boundaries of complexity and innovation? Look no further than Rotec! With our expertise in CNC machining across a wide range of materials, including metals, plastics, composites, and exotic alloys, we are equipped to meet your most demanding requirements with precision and excellence. Whether you're in the aerospace, automotive, medical, or any other industry, our team stands ready to collaborate with you to bring your vision to life. To discuss your project,
contact us today!
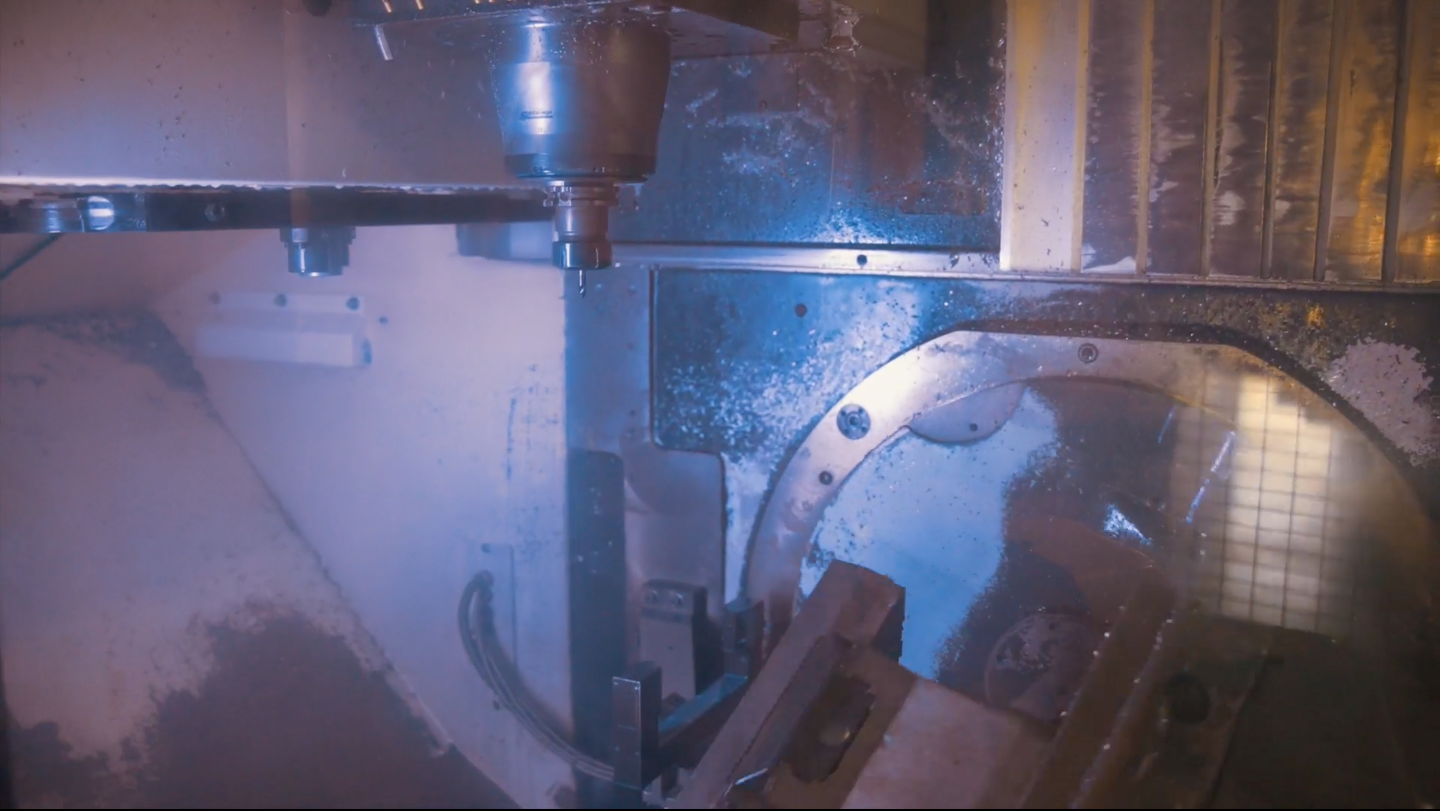
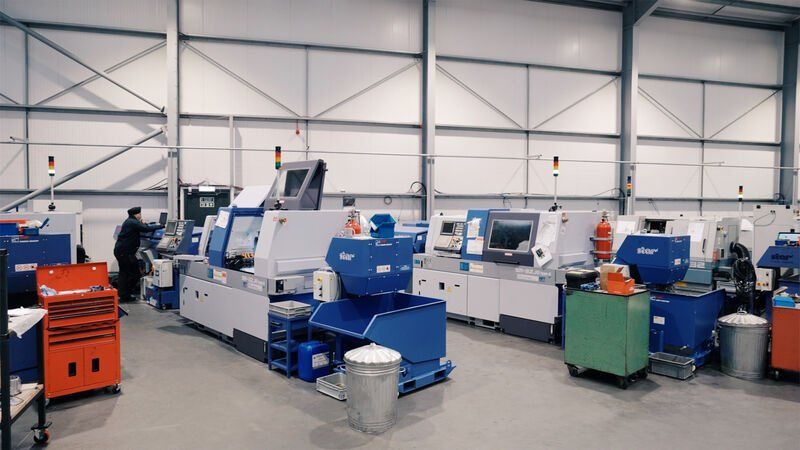
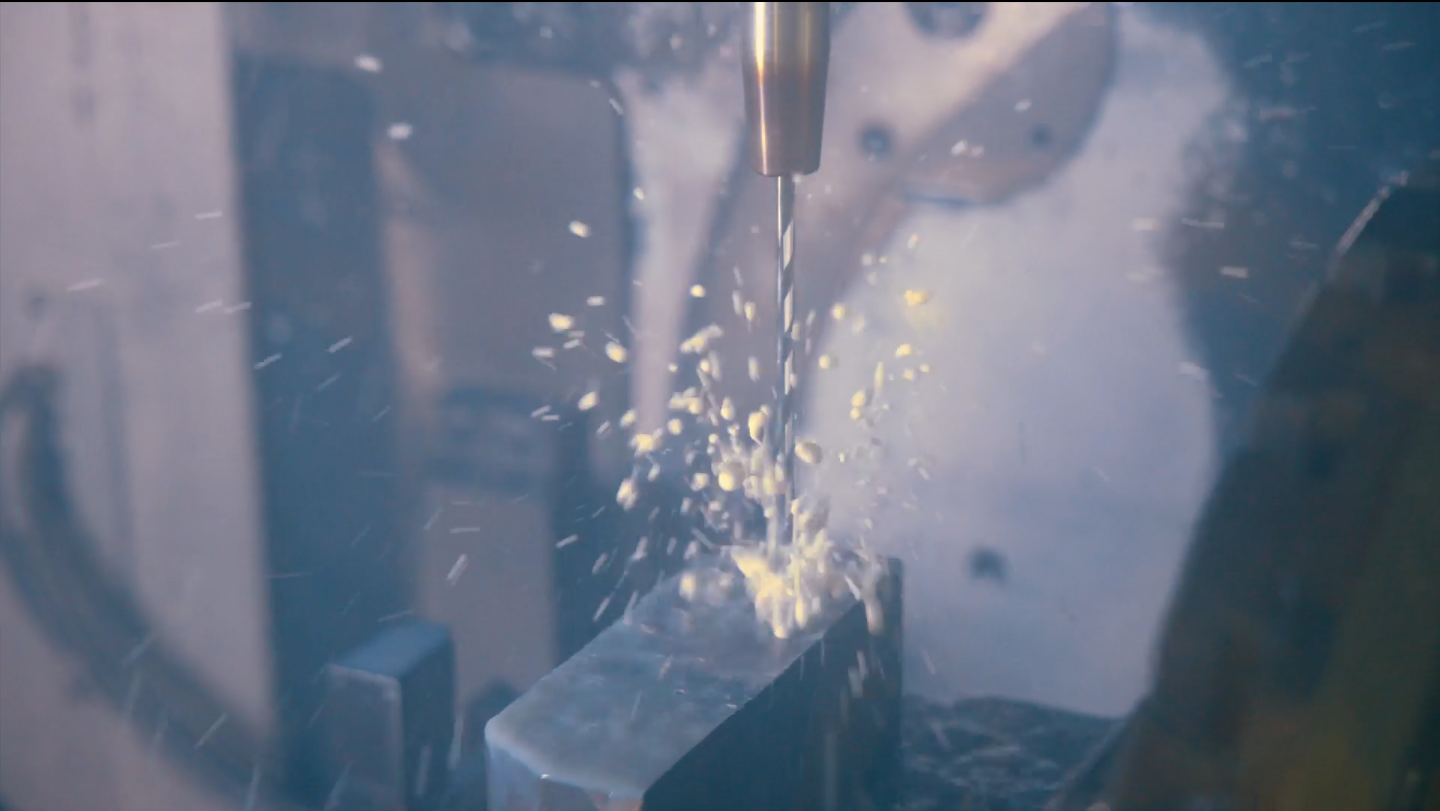
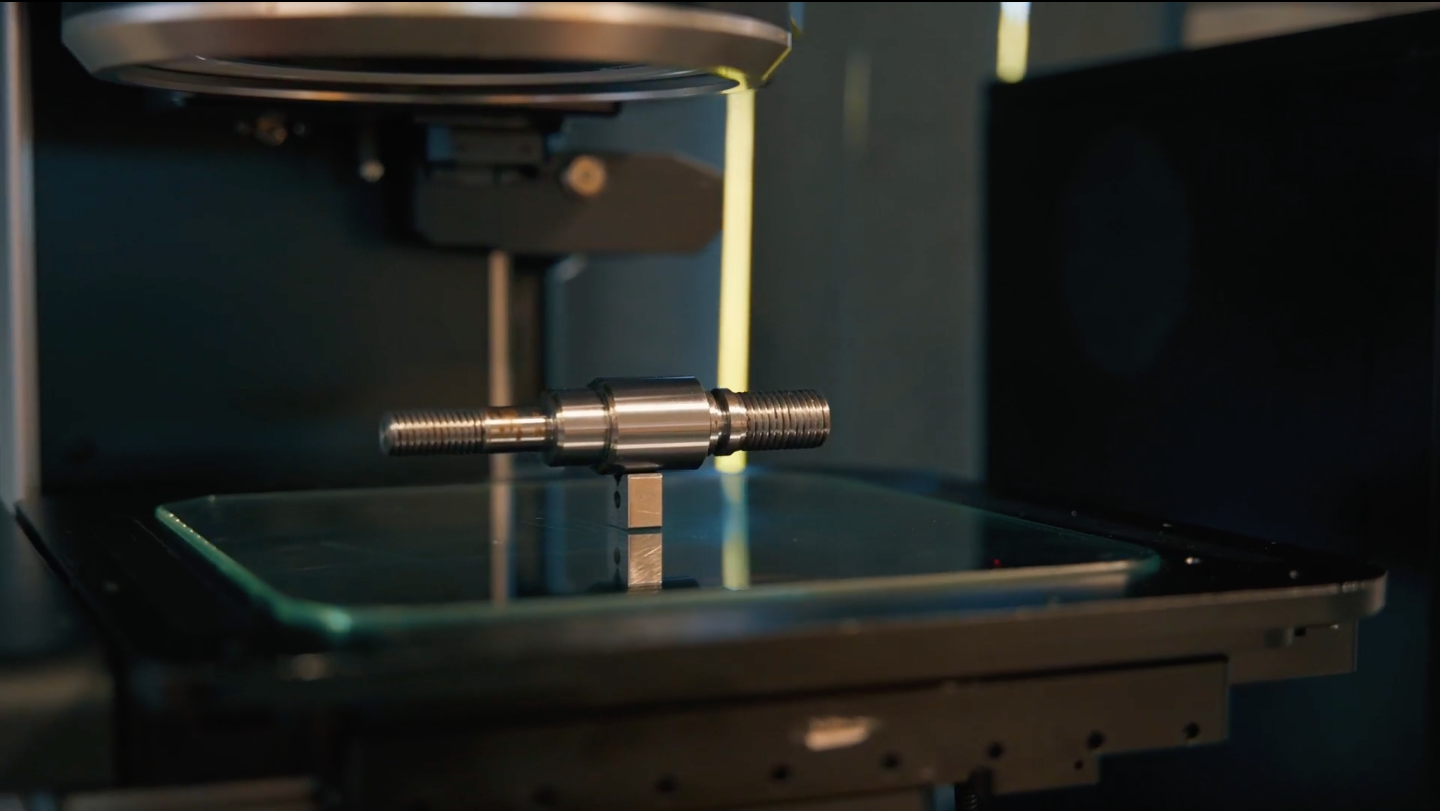