~ Understanding the uses and benefits of CNC machinery ~
Having a better idea of CNC machine operations helps professionals stay competitive in a rapidly evolving manufacturing landscape.
This is a guide about CNC machinery. CNC machinery has many different uses, but it is important to understand the features and benefits and how to choose the correct CNC machinery for the specific needs of your business.
What is CNC machining?
CNC machining is a manufacturing process that is subtractive. It is used to create parts of components in a process where material is removed from the workpiece or stock. The functionality comes from pre-programmed software and codes that are fed into the machine and controls the movement of the CNC machinery. You’ll find a wide range of machinery that comes under the umbrella of CNC machining, such as plasma-cutting machines, grinders, lathes, and turning mills.
What is possible with CNC machining?
The following are manufacturing possibilities with CNC machining:
- Rapid prototyping
- Production
- Tooling
- Hybrid manufacturing
- Electrical discharge machining (EDM)
What industries use CNC machinery?
CNC machining is used within a wide range of industries, such as:
Aerospace industry
CNC machining is used to manufacture components for metal aircraft and other engineering components. Precision is crucial within this sector, as is reliability.
Automotive industry
CNC machining is used to manufacture both prototypes and full-blown production runs. You’ll find it used within the manufacture of cylinder blocks, gearboxes, axels, valves, and other components.
Electronics
Laptops, smartphones, and any other type of consumer electronics utilise the precision of CNC machinery to produce prototypes and full product parts
Military
The military sector uses CNC machines for the prototypes of reliable parts, helping to map out parts that will be required to withstand heavy wear and tear. There is overlap between this sector, aerospace and electronics.
Healthcare
Medically-safe materials and precise components for medical equipment require tight tolerances that only CNC machining can offer.
Oil and gas industry
Another industry that requires tight tolerances for safety purposes is the oil and gas industry. CNC machining is used to manufacture precise and reliable parts such as valves, pins, rods, cylinders, and pistons.
Preparing for CNC Machine Operations
What is the importance of CNC machining?
CNC machining offers an integral part of the modern industrial environment. This is due to the ability to produce accurate shapes that can be repeated on a large-scale in a fast, safe, and affordable way. It is a method that enables the fabrication of items and products that might otherwise be too expensive to manufacture in large quantities, such as microwave tower parts, amplifier housings, and heat sinks for telecommunications equipment. Intricate, complex components and parts can be manufactured with precision, to whatever scale of production is required.
How to choose a CNC machine
There are a few different metrics that you should use when choosing the correct CNC machine for your task and purposes.
Consider the project goal
The first thing is to consider what the goal of the task is. There is a different optimal CNC machine required to work on metal than there is to work with wood, for instance.
The project costs
Always bear in mind the costs of the project that you have to work with. This should include the cost of running the machine itself, all labour costs and maintenance.
Weight of the machine
The weight of the CNC machine comes into play depending on the type of materials that are being worked with. For heavy-duty materials, a heavier machine is required.
Power requirements
The power rating of the equipment is important as this will also help to provide an accurate estimation of power and cost requirements for the machine and task.
What are the benefits of CNC machinery?
There are a few benefits to CNC machinery that make it a good choice for a wide range of tasks and applications;
Minimal waste
CNC is efficient in material waste. This is due to the characteristics of precision and accuracy. If the software and algorithm side of the task is properly designed, then there are almost never any faulty cuts, which is what would lead to material waste. Precision cuts and angles offer efficiency not just for the end product but for the lack of waste too.
Accuracy
The accuracy of CNC machines is a key selling point. The machines receive instructions from a computer, aiding accuracy of movement and cutting action. Every single time the process is underway will be identical to the last time, and the next time. This allows for the creation of parts and components with tight tolerances, and almost completely eliminates human error.
Rapid production technique
Alongside the precision it provides, CNC machining also does so at speed. This allows for components and parts to be produced at scale, without diminishing levels of accuracy and efficiency. This leads to much faster completion of project targets and means continuous production that isn’t possible with manual labour.
Fast assembly potential
The precision and consistency of a part made by a CNC machine results in a much easier assembly process for the finished parts. No matter what section of the production run a component has been manufactured in, it will consistently fit together exactly with parts from another section of the run, the same way as it does on the computer. This helps to save time and money in the assembly process.
Reduces safety risks
The automation of the machining process helps to minimise or eliminate many inherent safety hazards and challenges that are present when working with manual processes. CNC machines are usually enclosed, reducing the risk of injury even further.
Lower energy consumption
Compared with traditional processes, CNC machining uses less electricity. Reducing energy consumption and helping to reduce the carbon footprint of the project and company overall. This is due to the fast-paced nature of CNC machines and the fact it draws less power per minute than other methods of manufacturing.
Lower production costs
The precision and efficiency of CNC machining in manufacturing parts and components leads to fewer raw materials being used to create the finished product. By focusing on CNC machining, you are entering a more economical way of manufacturing, reducing errors, lowering expenditure and product costs.
CNC machining provides a reliable, accurate, and safe way to manufacture parts and components for a wide range of applications and industries.
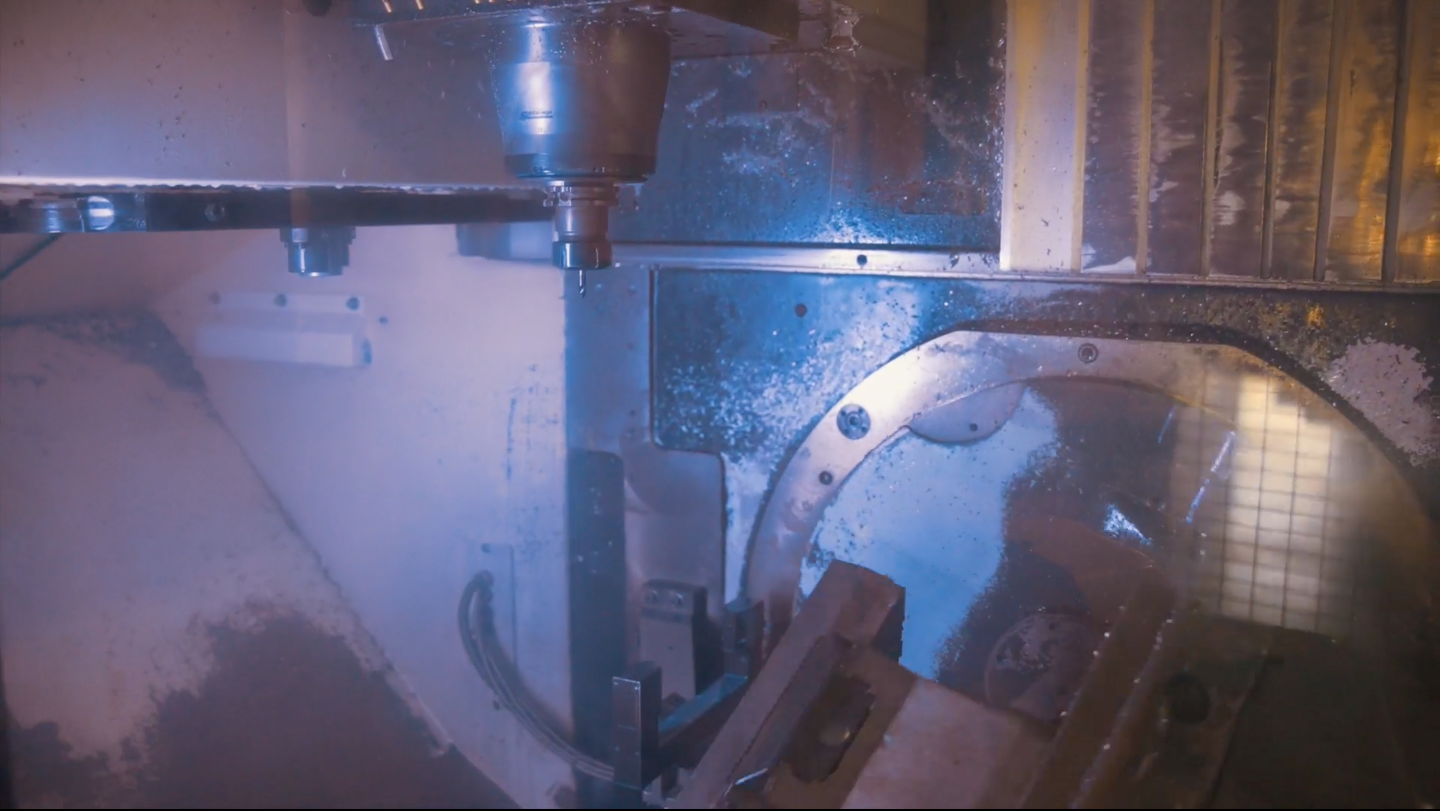
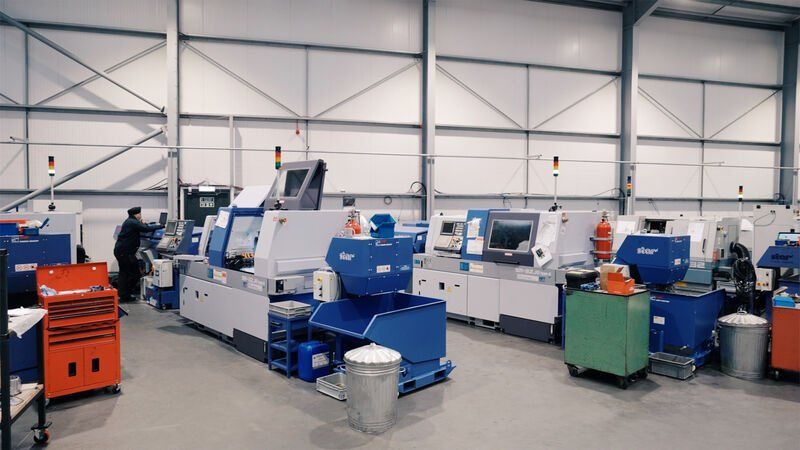
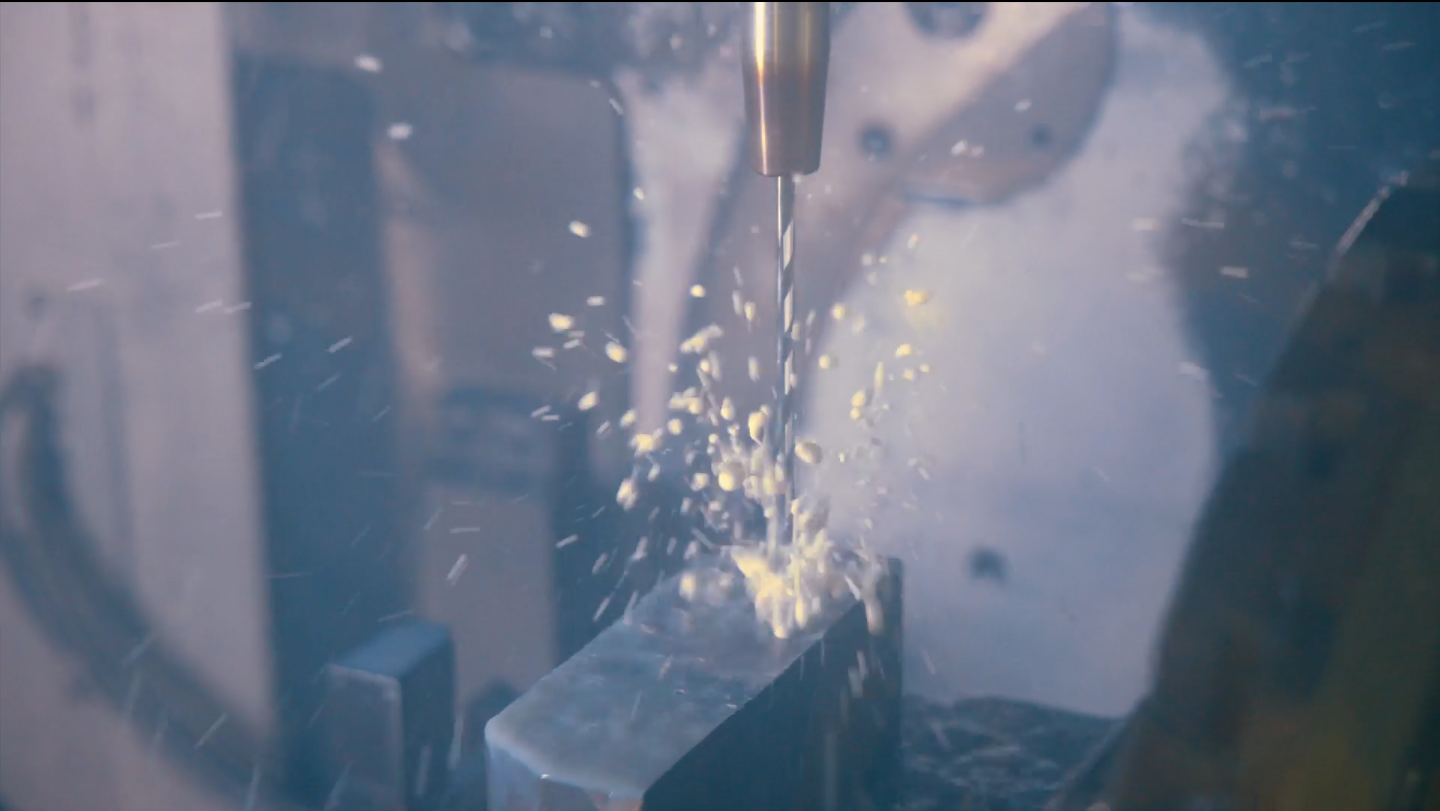
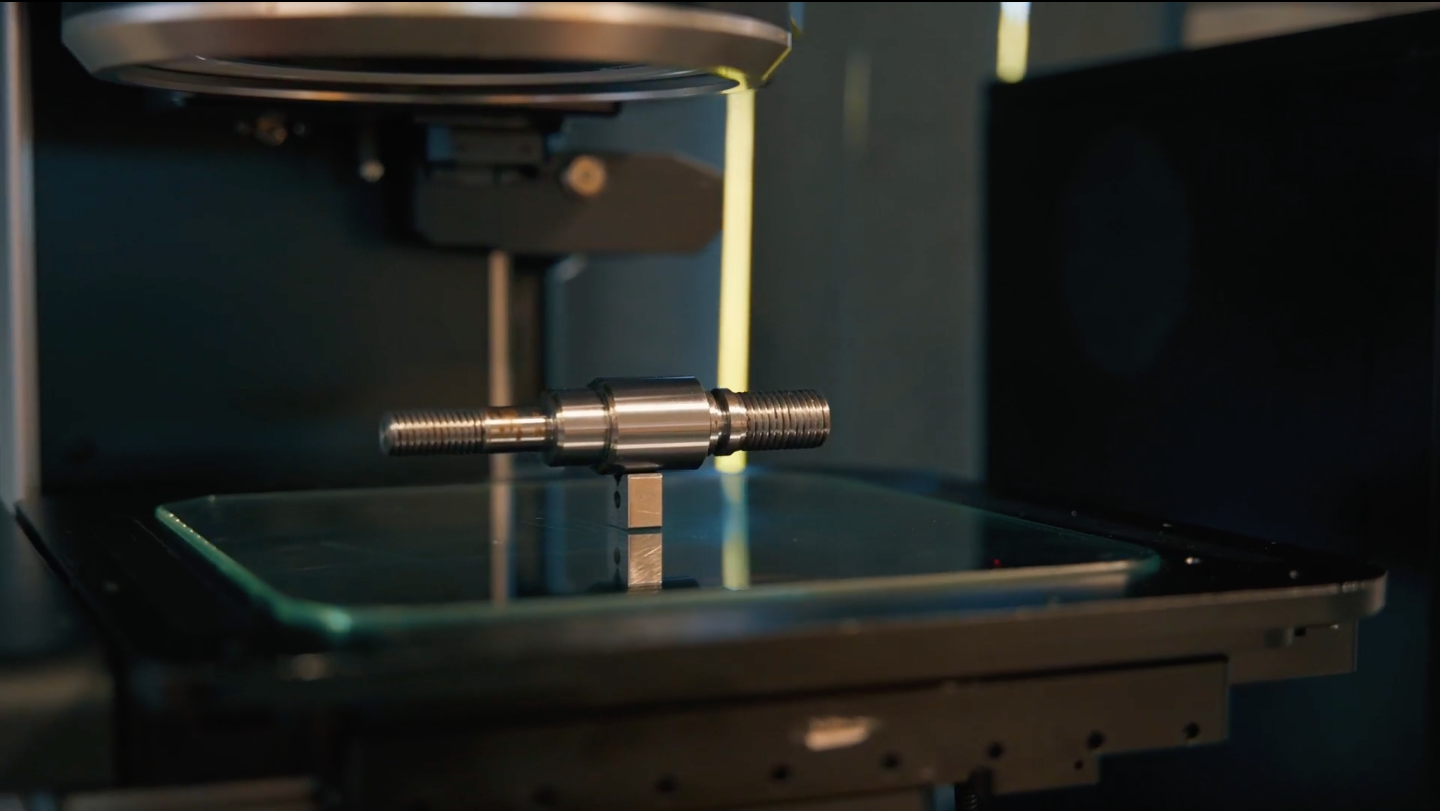