~ What is CNC threading? ~
CNC threading is an application that is widely used within the wider CNC machining world. It is a subtracting approach that creates different diameters for both internal and external threads. The rotating tool is calibrated with a thread depth and density that is desired and moved in a circular motion to produce the end result. The structure of the CNC thread machine consists of different pieces, and we’ll explore that in greater detail.
Why threads are important
Wherever there is a screw present in a machined part, they remain an important part of the overall metalwork. A thread is designed to couple two systems together, with the motion between the two pieces happening during the coupling process. This is a way of facilitating the connection of different parts in a low-cost, fast, and efficient way. It makes them an essential component for fittings, fasteners, and connectors. There are different types of threads that are suitable for different projects and applications, so it is important to understand what your project needs.
The quality and efficiency of the CNC machining is important, as this will have a direct impact on the threads produced and the efficiency of the production process. As the technology used within CNC machining improves, the consistency and accuracy of the threading process improves with it.
What are the different thread parts?
The following are the different parts of the thread:
Helix Angle
This is the angle between the helix in the straight thread and the thread axis, or the angle made by the conical helical area of a thread when looking at taper threads.
Root
The bottom of the thread which is adjacent to the projected cone or cylinder.
Crest
The top of the threads, this is the farthest area of the projected cone or cylinder, and the surface which joins the flanks.
Flank
The connection of the root to the crest.
Pitch
The diameter of the cone or cylinder equals the diameter of the pitch. This is the distance between the areas on adjacent threads, and any parallel areas must measure the same.
Are there different types of machining threads?
Although there are myriad types of specific threads when looking at classification standards, there are two major types of thread that it is important to understand:
Internal threads
The female thread, internal threads are machined using a single-lip threading tool. An internal thread is required if your workpiece needs screw insertions. Apart from the single-lip tool, a threading cap can also help to cut CNC internal threading. Internal threads can only be cut on a concave surface
External threads
A screw thread is used in the application of bolts, studs, screws, and plug gauges. A lathe is used to make external threads most commonly, as it is an effective process. Another method is where a round die is used to cut the thread by hand, as well as hexagonal square dies where there is a need for interlocking use.
How to cut a thread?
Thread cutting is perfect for parts where there will be a requirement for screwed connections. Understanding the process for cutting threads is beneficial within this type of manufacturing. It is important to understand the diameter of the hold that the thread is to be placed in once manufactured. To determine the diameter of the core hole, take the tap diameter and subtract the thread pitch from it.
For an internal thread, start by finding the centre with a punch, before drilling the core hole with a twist drill. The use a 90-degree countersink to make a chamfer into the core hole. You then turn the tap wrench into the core hole with the tap attached. For an external thread, first file the edges of the round rod, and chamfer it at a 45 degree angle. The chamfer must be bigger than the depth of the thread. You must then clamp or grip the round die to firmly affix it, as there is a lot of pressure applied to cut the external thread in the best way possible.
What are common methods for CNC machining thread
There are different CNC methods for screw thread machining, including:
Tapping
Tapping holes are commonly used when producing internal threads, as it is an economical and efficient way to thread. It is a CNC method that is primarily used where there are holes with a small diameter. CNC threading offers reduced downtime, and there is a simple machining structure when compared with other methods. Tapping offers a fast cutting process which significantly boosts productivity and efficiency.
Thread milling
Another method is thread milling, where a milling cutter is used with a 3-axis machining centre. A circular interpolation of the three main axes is also adopted. This CNC method is perfect for materials that have a high value or where there are large parts to work with. The speed is fast, with precision levels high and efficiency levels increased. Milling cutter tools are versatile, robust, and reduce the need for many different tools, as the same cutter can be used for the left and right-hand threads, and it is simple to adjust the diameter of holes, tolerances, and materials cut.
Lathes
Lathes are another common way to cut threads, with a CNC lathe used to produce high quality screw threads. Machinists of a CNC lathe has the ability to make tapered threads, lead threads, and thread pitches. Within CNC lathe threading you’ll see rigid tapping and single-point threading that uses an indexable insert that can be set to correspond with the finished screw head.
Grinding
Where there is a need for hardened workpieces, thread grinding is an ideal CNC method. There are two different types of grinding wheels that are commonly used within this process, multi-line grinding wheels and single-line grinding wheels. Single-line is the better choice for making a screw with precision.
CNC machining threading is a vital part of the manufacturing process for many different products. Understanding the different types of processes and potential for end-result screws and other applications is important to make the right machining decisions.
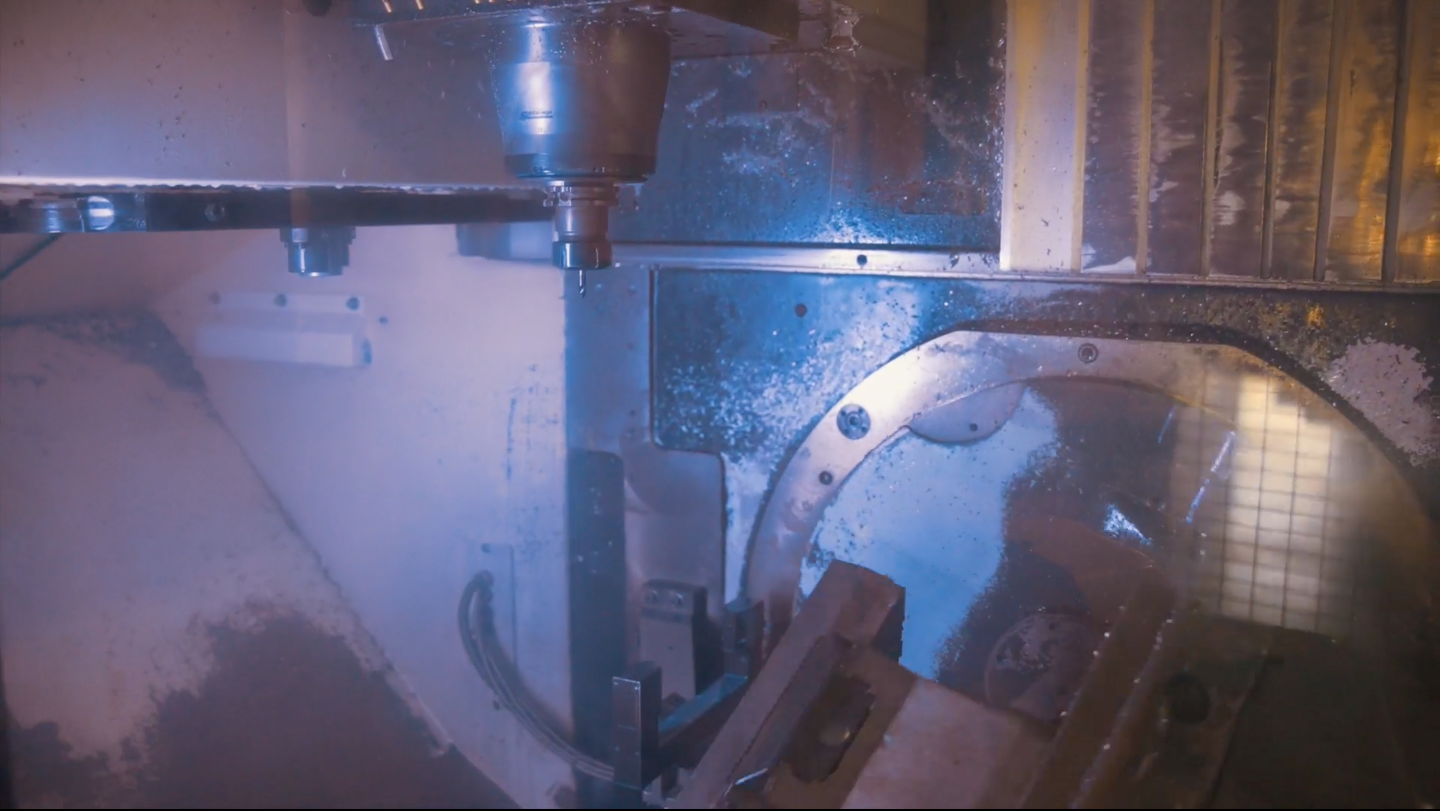
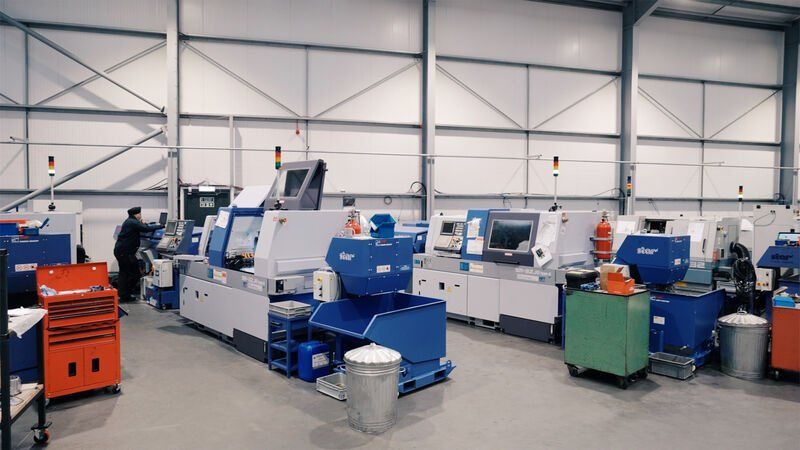
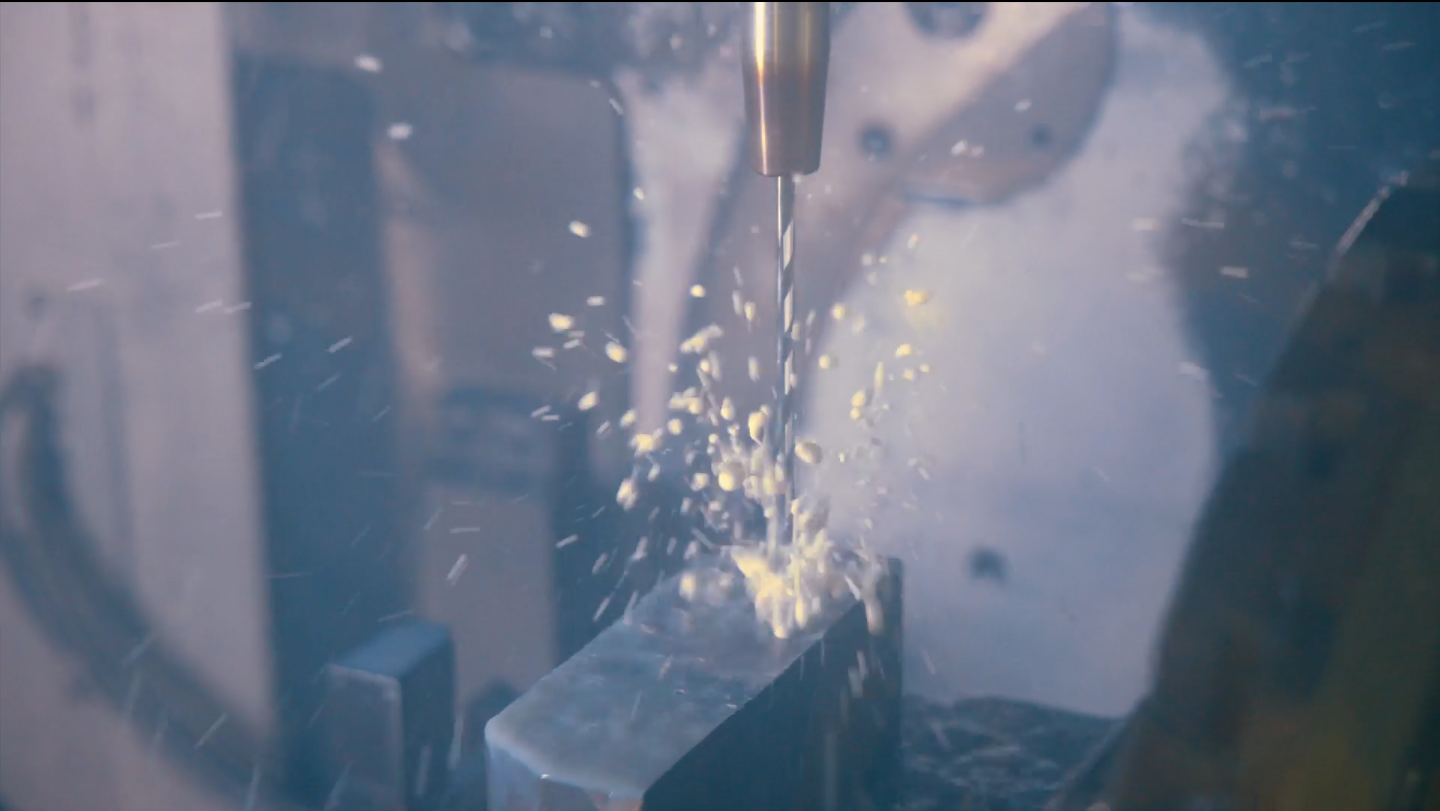
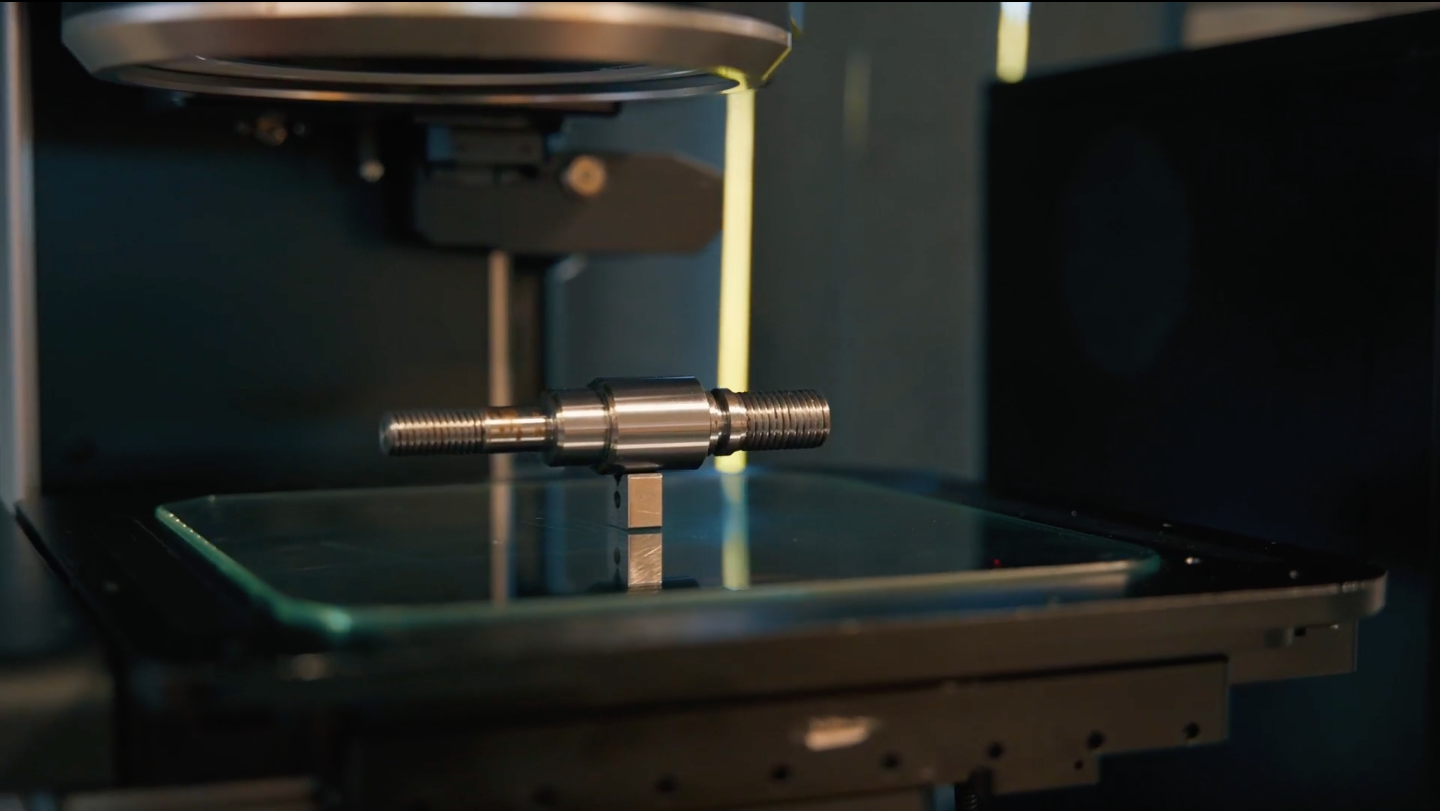