~ An Inside Look at CNC Precision Machining ~
CNC Precision Machining has revolutionised how we create everything, from everyday consumer goods to advanced aerospace components.
CNC machining has played an important role in industrial development for more than a few decades, evolving from manual craftsmanship to highly automated processes. The leap from manually operated machines to sophisticated computer-controlled systems has transformed manufacturing, enabling unprecedented levels of accuracy and efficiency. In fact, CNC Precision Machining has revolutionised how we create everything, from everyday consumer goods to advanced aerospace components.
If you are interested in learning more about
CNC Precision Machining and the role it plays in modern manufacturing and engineering, you have come to the right page! In this article, we will delve into the intricacies of CNC precision machining, how it works, its common applications, advantages and challenges associated with this form of technology and much more. But before we dive in, let's understand what CNC precision machining is and what makes it an essential part of modern manufacturing processes.
What is CNC Precision Machining?
CNC precision machining refers to the process of using computer-controlled tools to shape and create parts with high precision. Unlike traditional machining methods, which rely heavily on manual input, CNC precision machining utilises pre-programmed computer software to control the movement of machinery and tools. This allows for the production of complex parts with consistency and accuracy, making it an essential technology in the field of modern manufacturing and precision engineering.
The impact of CNC precision machining spans numerous industries, from automotive and aerospace to medical devices and electronics. Its ability to produce intricate components with high precision makes it invaluable for applications requiring tight tolerances and superior quality. This technology not only improves production capabilities, but also supports innovation, enabling the creation of products that were previously difficult to manufacture with high precision, using traditional methods.
How CNC Precision Machining Evolved Over Time
The mid-20th century saw the introduction of numerical control (NC) machines, which used punched tape to control machine movements. This innovation laid the groundwork for CNC technology. With the development of computers, these machines evolved into CNC systems, offering enhanced precision, repeatability, and automation. The integration of CAD (Computer-Aided Design) and CAM (Computer-Aided Manufacturing) further revolutionised the process, allowing for more complex and intricate designs.
The evolution of machining techniques during the Industrial Revolution propelled mass production and significantly boosted manufacturing efficiency. CNC machining, building on these advancements, has taken industrial capabilities to new heights. By automating and streamlining production processes, CNC machining has not only improved the quality and consistency of manufactured parts, but has also enabled the creation of innovative products across various sectors.
The Basics of CNC Precision Machining
At the core of CNC precision machining lies the concept of Computer Numerical Control or CNC. CNC involves the use of computer systems to control the movement and operation of machinery. The process of CNC machining begins with the digital design of the product to be created, typically developed using CAD software. This design is then converted into a set of instructions that the CNC machine follows to produce the desired part with high precision.
Components of a CNC Precision Machining System
A typical CNC machining system comprises several key components:
- Machine Tool: The primary device used to shape the material. Common types include lathes, mills, and routers.
- Control Unit: The computer system that interprets the CAD/CAM instructions and controls the machine tool.
- Actuators and Motors: Devices that move the machine tool along predefined paths with precision.
- Cutting Tools: The implements that actually perform the cutting, drilling, or shaping of the material.
- Workpiece: The raw material that is being machined into a final product.
Working Principles and Processes Involved in CNC Precision Machining
CNC precision machining involves several steps to transform a digital design into a physical part:
- Designing: Engineers create a detailed digital model of the part using CAD software.
- Programming: The digital design is converted into G-code, a language that CNC machines understand.
- Setup: The machine is prepared, including mounting the workpiece and selecting the appropriate cutting tools.
- Machining: The CNC machine executes the programmed instructions, moving the cutting tools precisely to shape the material.
- Finishing: After machining, additional processes such as grinding, polishing, or coating may be applied to achieve the desired finish.
By automating these steps, CNC precision machining ensures high levels of accuracy, repeatability, and efficiency.
How CNC Machining Achieves Precision
Tools and Techniques for Achieving Precision
CNC precision machining employs a variety of tools and techniques to achieve high levels of accuracy. Key tools include end mills, drills, and lathes, each designed for specific cutting and shaping tasks. These tools are made from materials like high-speed steel, carbide, and diamond, ensuring durability and precision. Techniques such as multi-axis machining allow the tools to move along multiple axes simultaneously, to enable the creation of complex geometries and detailed features that would be almost impossible to create using simpler, single-axis machines.
Role of CAD and CAM in CNC Precision Machining
The integration of CAD (Computer-Aided Design) and CAM (Computer-Aided Manufacturing) is crucial in CNC precision machining. CAD software is used to create detailed 3D models of the parts to be manufactured, along with precise dimensions and specifications. These models are then imported into CAM software, which generates the G-code instructions that guide the CNC machines. This seamless transition from digital design to physical production ensures that the final product adheres to the original specifications, minimising errors and improving overall accuracy.
Quality Control Measures
Maintaining precision in CNC machining requires stringent quality control measures. These include:
- Machine Calibration: Regular calibration of CNC machines ensures that they operate within specified tolerances.
- Tool Inspection: Tools are routinely inspected for wear and tear to maintain cutting accuracy.
- In-Process Monitoring: Advanced sensors and monitoring systems track the machining process in real-time, detecting and correcting deviations immediately.
- Post-Production Inspection: Finished parts undergo thorough inspections using tools like coordinate measuring machines (CMMs) to verify dimensional accuracy and quality.
Advantages and Challenges of CNC Precision Machining
Advantages
CNC precision machining offers several advantages over traditional machining methods:
- Accuracy and Consistency: CNC machines can produce parts with extremely high precision and repeatability, reducing the likelihood of human error.
- Efficiency: Automation and high-speed operation increase production rates and reduce lead times.
- Flexibility: CNC machines can be quickly reprogrammed to produce different parts, making them ideal for both high-volume production and small batches.
- Complexity: CNC machining can create intricate geometries and detailed features that are difficult or impossible with manual methods.
Challenges and Limitations
Despite its advantages, CNC precision machining faces several challenges:
- Initial Costs: The upfront investment in CNC machinery and software can be high, making it a significant expenditure for small businesses.
- Maintenance and Training: Regular maintenance and skilled operators are essential to keep CNC machines running smoothly and efficiently.
- Material Limitations: While CNC machines can work with a wide range of materials, some materials may pose challenges due to hardness, brittleness, or other properties.
The Role of Skilled Workforce in CNC Precision Machining
CNC precision machining relies heavily on a skilled workforce to operate and maintain the machines. Operators must have a deep understanding of both the mechanical and software aspects of CNC systems. This requires comprehensive training in areas such as CAD/CAM software, machine operation, and programming. Vocational schools, apprenticeships, and on-the-job training programs are essential for developing the expertise needed in this field. Continuous education is also important, as advancements in technology require operators to stay updated with the latest practices and tools.
While CNC machining is highly automated, the role of human craftsmanship remains crucial. Skilled machinists are responsible for setting up machines, fine-tuning processes, and ensuring that the final products meet exacting standards. Their expertise is vital in troubleshooting issues, making real-time adjustments, and maintaining the overall quality of production. The combination of advanced technology and human craftsmanship ensures that CNC machining achieves the highest levels of precision and efficiency.
Sustainability and Environmental Impact of CNC Precision Machining
High Efficiency and Resource Optimisation
CNC precision machining is inherently efficient, especially when it comes to optimising resource use and reducing waste. The precision of CNC machining ensures that materials are cut and shaped with minimal excess, thereby reducing the requirement for raw materials. This efficiency translates into not just cost savings, but also a reduced environmental footprint.
Waste Reduction and Recycling Efforts
One of the significant advantages of CNC precision machining is its ability to minimise waste. Traditional machining methods often generate substantial scrap material, but CNC machines are programmed to cut with high precision, leaving less excess material. In addition to this, many manufacturers implement recycling programs for the metal chips and scrap produced during the machining process. These recycling efforts not only reduce waste, but also promote a circular economy within the manufacturing sector.
Low Energy Consumption and Carbon Footprint
CNC machines, while energy-intensive, can contribute to a lower overall carbon footprint through their efficiency and precision. Modern CNC equipment is designed to be energy-efficient, using advanced technologies to reduce power consumption during operation. Additionally, the precise nature of CNC machining means that parts often require fewer subsequent processing steps, which can further reduce energy use. As the industry advances, incorporating renewable energy sources and more energy-efficient practices can further mitigate the environmental impact of CNC machining.
Applications of CNC Precision Machining Across Industries
Automotive Sector
In the automotive industry, CNC precision machining plays a critical role in producing engine components, transmission parts, and complex body structures. The high level of precision ensures that parts fit together seamlessly, enhancing vehicle performance and safety. CNC machining also allows for rapid prototyping, enabling manufacturers to quickly develop and test new designs.
Aerospace Industry
The aerospace industry demands components with extremely tight tolerances and high reliability. CNC precision machining meets these requirements by producing parts such as turbine blades, aircraft frames, and landing gear components with unmatched accuracy. The ability to work with advanced materials like titanium and composites further expands its applications in aerospace engineering.
Medical Field
CNC precision machining is vital in the medical field, where it is used to manufacture surgical instruments, prosthetic devices, and diagnostic equipment. The precision and consistency of CNC machining ensure that medical devices meet stringent regulatory standards and perform reliably in critical applications.
Electronics and Consumer Goods
In the electronics industry, CNC machining produces intricate components for smartphones, computers, and other consumer electronics. The ability to create parts with fine details and tight tolerances is essential for the miniaturisation of electronic devices. Similarly, in the consumer goods sector, CNC machining enables the production of high-quality, aesthetically pleasing products with complex designs.
Future Prospects and Innovations in Precision Engineering
The future of CNC precision machining is bright, with ongoing advancements in technology poised to enhance its capabilities further. Innovations such as artificial intelligence, machine learning, and the Internet of Things (IoT) are expected to improve automation, predictive maintenance, and process optimisation. Furthermore, the development of new materials and cutting tools will continue to expand the applications and efficiency of CNC machining in various industries.
Final Thoughts
While CNC precision machining is a highly technical field, it is also a craft that requires skill, knowledge, and dedication. The machinists who operate these sophisticated machines play a crucial role in transforming digital designs into physical products. Their expertise ensures that the highest standards of quality and precision are met, contributing to the success of countless industries. As we move forward in the age of modern manufacturing, recognising and valuing the craftsmanship behind CNC precision machining will remain essential for continued innovation and excellence in manufacturing.
At Rotec, we pride ourselves on our expertise in precision engineering and manufacturing, specialising in complex CNC machining tailored to meet the specific needs of various industries. Our skilled team, state-of-the-art technology, and commitment to quality ensure that we deliver superior solutions for your most challenging projects. To learn more about the solutions we offer and discuss your projects,
contact us today!
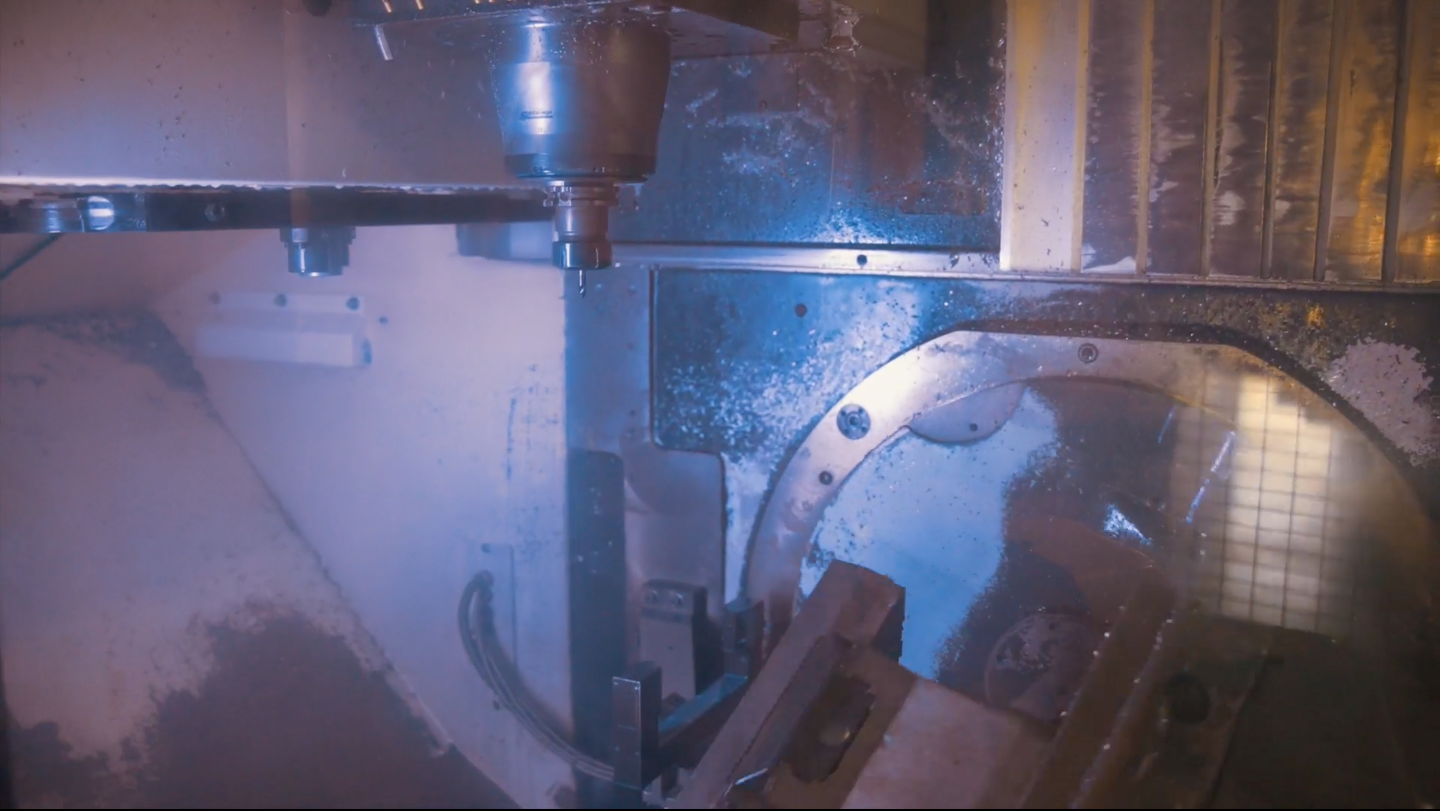
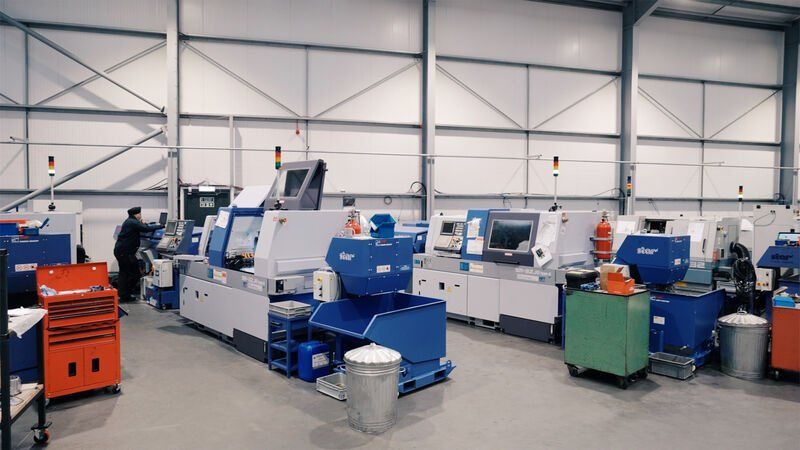
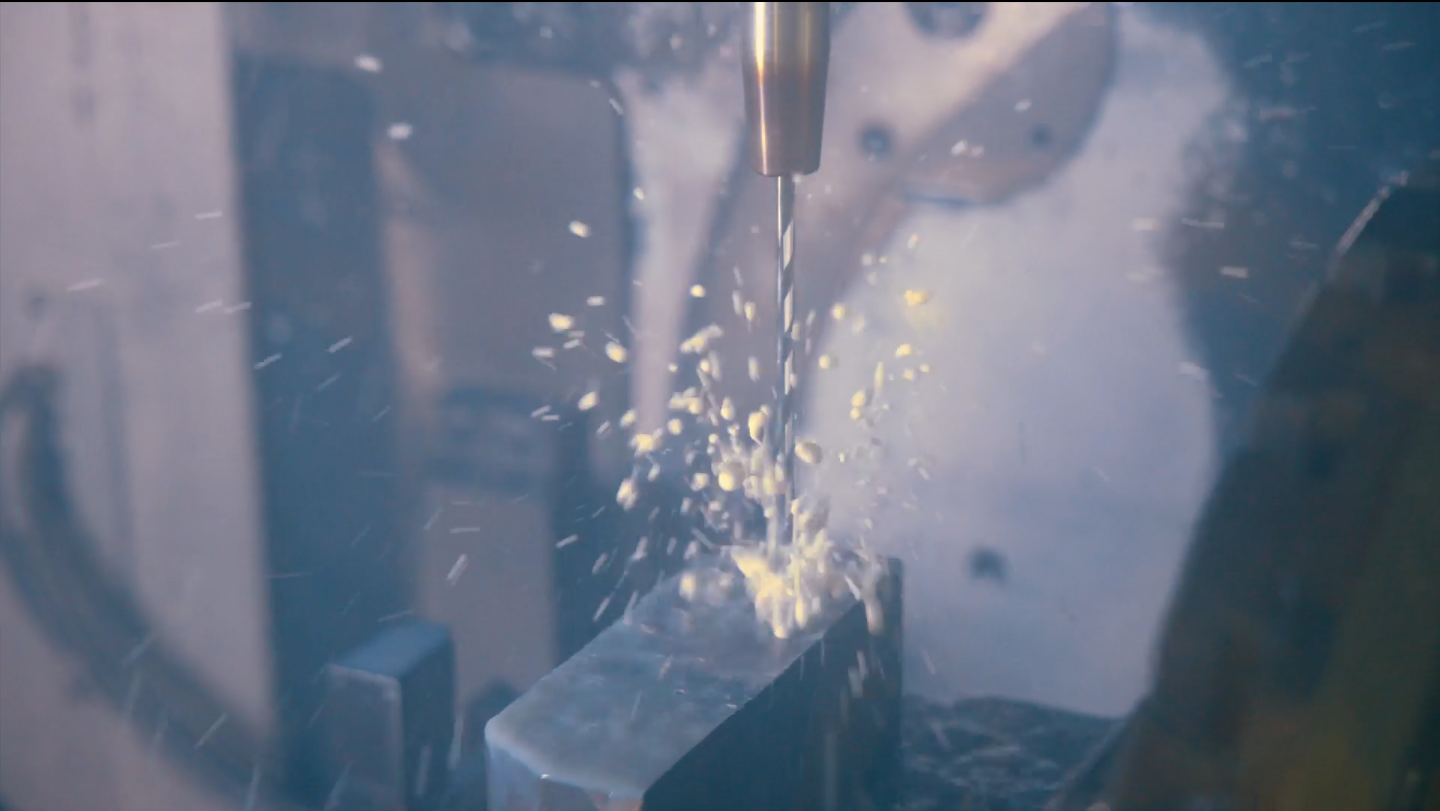
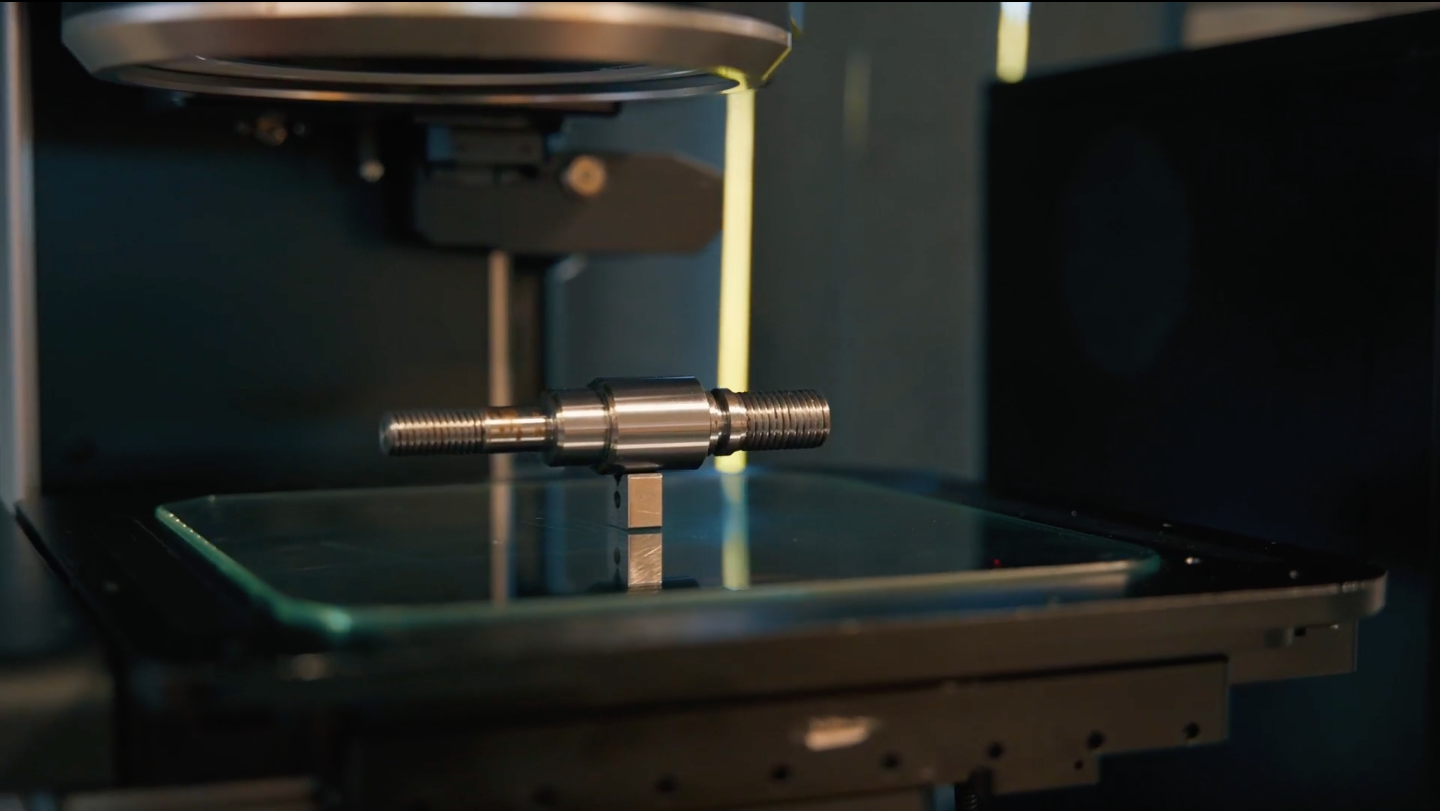