~ Comparing 4-Axis and 5-Axis Machining Methods ~
4-axis and 5-axis CNC machining have emerged to tackle intricate designs and complex geometries. But, how do they differ?
CNC (Computer Numerical Control) machining has revolutionized manufacturing processes, enabling precise and automated production of complex parts. Within the realm of CNC machining, 4-axis and 5-axis machining have emerged as advanced techniques to tackle intricate designs and challenging geometries.
If you are new to engineering and manufacturing or working on your product's design, you may be wondering what's the difference between the two and which one is better for your case. If that's so, you have come to the right page! In this article, we will delve into the world of 4-axis and
5-axis CNC machining, exploring their applications, differences, advantages, and when to choose one over the other. Let's start by looking into 4-axis CNC machining first.
4-Axis CNC Machining
4-axis CNC machining involves the utilization of a rotary table or indexer in addition to the traditional X, Y, and Z axes. This fourth axis enables the part to rotate, allowing access to multiple sides of the workpiece without requiring manual repositioning. This technique is particularly advantageous for producing complex surface geometries, multi-sided components, and intricate engravings or embossing.
Applications of 4-Axis CNC Machining:
Complex Surface Machining: Parts with contoured surfaces, such as mould cavities or artistic sculptures, benefit from the continuous toolpath enabled by the rotary axis.
Multi-Sided Parts: Components requiring machining on several sides, like engine blocks or aerospace structures, are efficiently processed without the need for multiple setups.
Engraving and Embossing: The fourth axis allows precise engraving and embossing on curved or irregular surfaces, ideal for branding, serial numbers, or decorative features.
Advantages and Disadvantages of 4-Axis CNC Machining:
Advantages:
- Enhanced Efficiency: Multiple sides of a part can be machined in a single setup, reducing cycle times and operator interventions.
- Reduced Setups: Eliminates the need for frequent repositioning of the part, minimizing setup time and errors.
Disadvantages:
- Limited Flexibility: Some geometries might require more than four axes to achieve complex machining, limiting the technique's applicability.
- Reduced Precision: The additional axis introduces complexity, potentially leading to diminished precision in certain cases.
5-Axis CNC Machining
5-axis CNC machining takes versatility to the next level by incorporating a fifth axis, usually a rotary or tilting spindle. This extra degree of freedom enables the tool to approach the part from virtually any angle, making it ideal for producing intricate, highly complex geometries.
Applications of 5-Axis CNC Machining:
Aerospace Components: Turbine blades, airfoils, and other aerospace parts often have intricate curved surfaces that can be efficiently machined using 5-axis techniques.
Medical Implants: Complex medical implant designs can be precisely manufactured with minimal material waste, meeting the stringent demands of biocompatibility.
Sculpture and Artistic Work: Artists can create intricate sculptures with intricate undercuts and intricate features, replicating their designs with high precision.
Advantages and Disadvantages of 5-Axis CNC Machining:
Advantages:
- Geometric Versatility: Unparalleled access to complex part geometries, including undercuts and compound angles, without repositioning.
- Reduced Setup Complexity: Multiple faces and angles can be machined in a single setup, saving time and enhancing accuracy.
Disadvantages:
- Increased Complexity: The higher number of axes demands advanced programming skills and sophisticated CAM software.
- Higher Cost: Machines equipped for 5-axis machining tend to be more expensive, requiring a significant investment.
In the next sections of this article, we will explore the key differences between 4-axis and 5-axis CNC machining, discuss factors for selecting the appropriate option, and provide real-world case studies to illustrate when each technique is the better choice.
Key Differences Between 4-Axis and 5-Axis CNC Machining
Number of Axes and Their Roles
4-Axis: Involves four axes (X, Y, Z, and an additional rotary axis), allowing access to multiple sides of a part through rotation.
5-Axis: Incorporates five axes (X, Y, Z, rotary, and often tilting spindle), providing unrestricted tool orientation for complex geometries.
Level of Complexity in Programming
4-Axis: Programming for four axes is less intricate compared to 5-axis machining, making it more accessible to a broader range of users.
5-Axis: Requires advanced programming skills due to the added complexity of toolpath generation for intricate angles and orientations.
Precision and Accuracy
4-Axis: While generally accurate, the additional rotary axis can introduce minor deviations in precision for certain geometries.
5-Axis: Offers higher precision and accuracy for complex parts, as the tool can approach the part from the most suitable angles.
Suitability for Different Part Geometries
4-Axis: Best suited for parts with multiple sides, contoured surfaces, and relatively simpler geometries.
5-Axis: Ideal for parts with intricate curves, undercuts, compound angles, and complex three-dimensional shapes.
4-axis vs. 5-axis: Selecting the Right Option for the Job
Part Complexity and Geometry
- For parts with intricate, compound geometries, 5-axis machining is the go-to choice to achieve precision and accuracy.
- Parts with straightforward geometries that require machining on multiple sides can be effectively produced using 4-axis machining.
Production Volume and Efficiency
- High-volume production of complex parts benefits from 5-axis machining, which minimizes setup times and maximizes throughput.
- Lower production volumes might find 4-axis machining more efficient, especially when the added complexity of 5-axis programming is unnecessary.
Budget and Investment Considerations
- If budget constraints are a primary concern, 4-axis machining offers a cost-effective solution while still catering to various geometries.
- Businesses willing to invest more upfront for the versatility of handling intricate designs should consider 5-axis machining.
Final Thoughts
When it comes to CNC machining, both 4-axis and 5-axis techniques play vital roles in addressing diverse manufacturing needs. Understanding the differences and advantages of 4-axis and 5-axis CNC machining empowers manufacturers to make informed decisions, aligning their choices with the demands of the task at hand.
If you are finding it challenging to identify the correct type of CNC machining for your needs and need expert advice and guidance, look no further! At Rotec, we have experience in identifying and implementing manufacturing solutions with a wide range of applications across various industries. To learn more about the topic or to connect with our CNC machining experts, contact us at
01386 424111 or
sales@rotec-ltd.com.
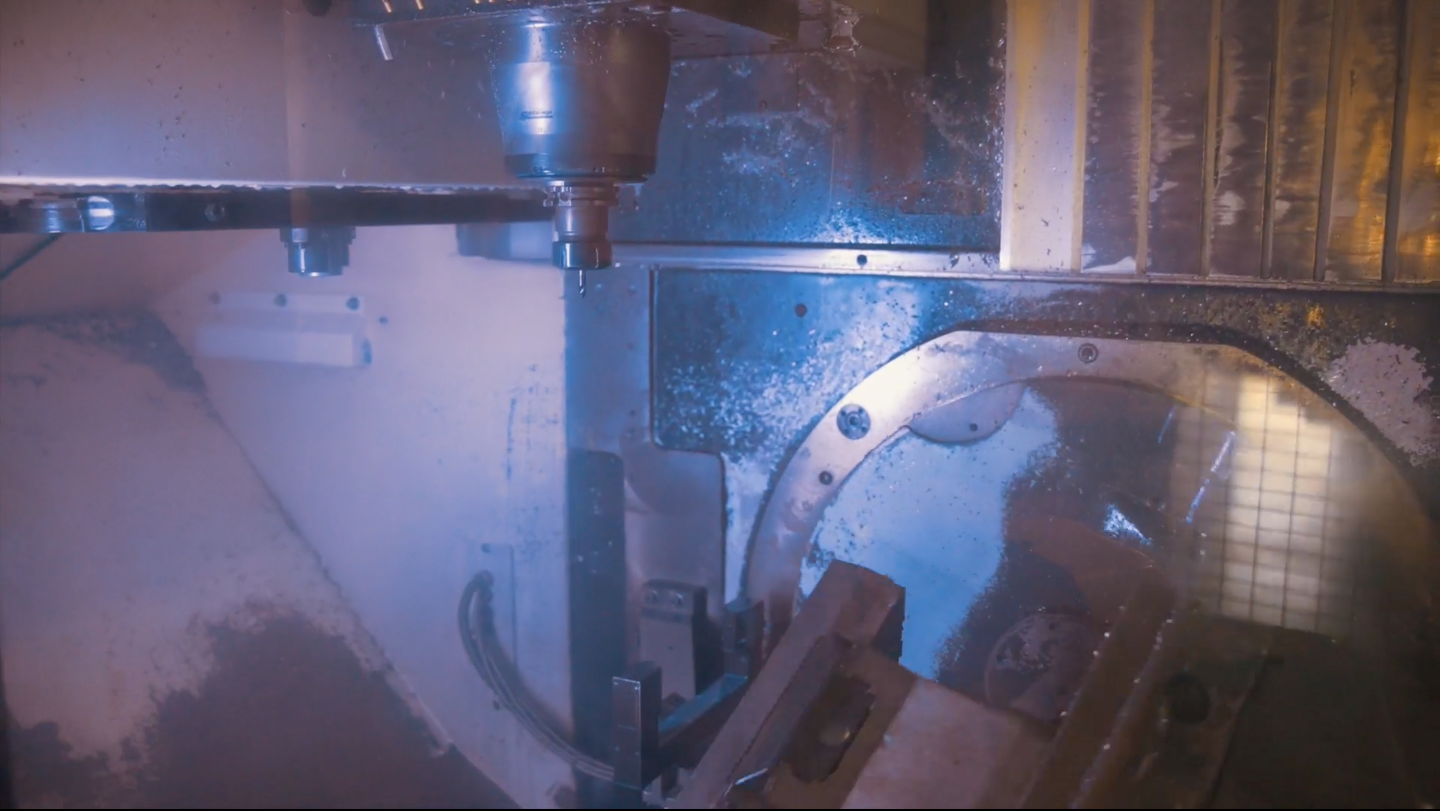
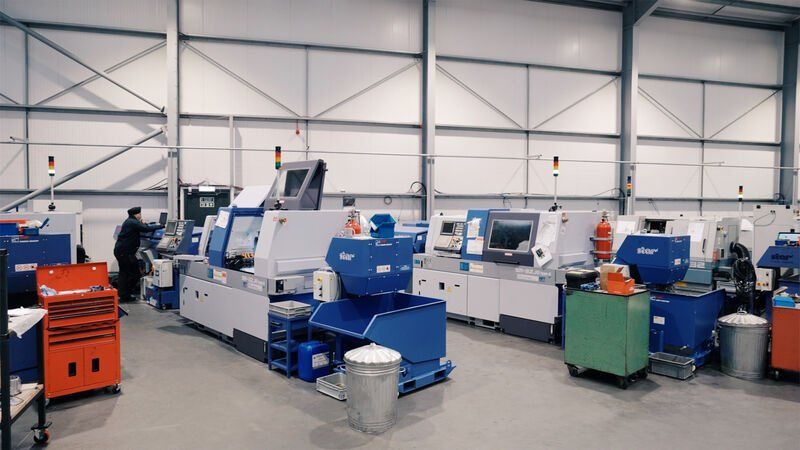
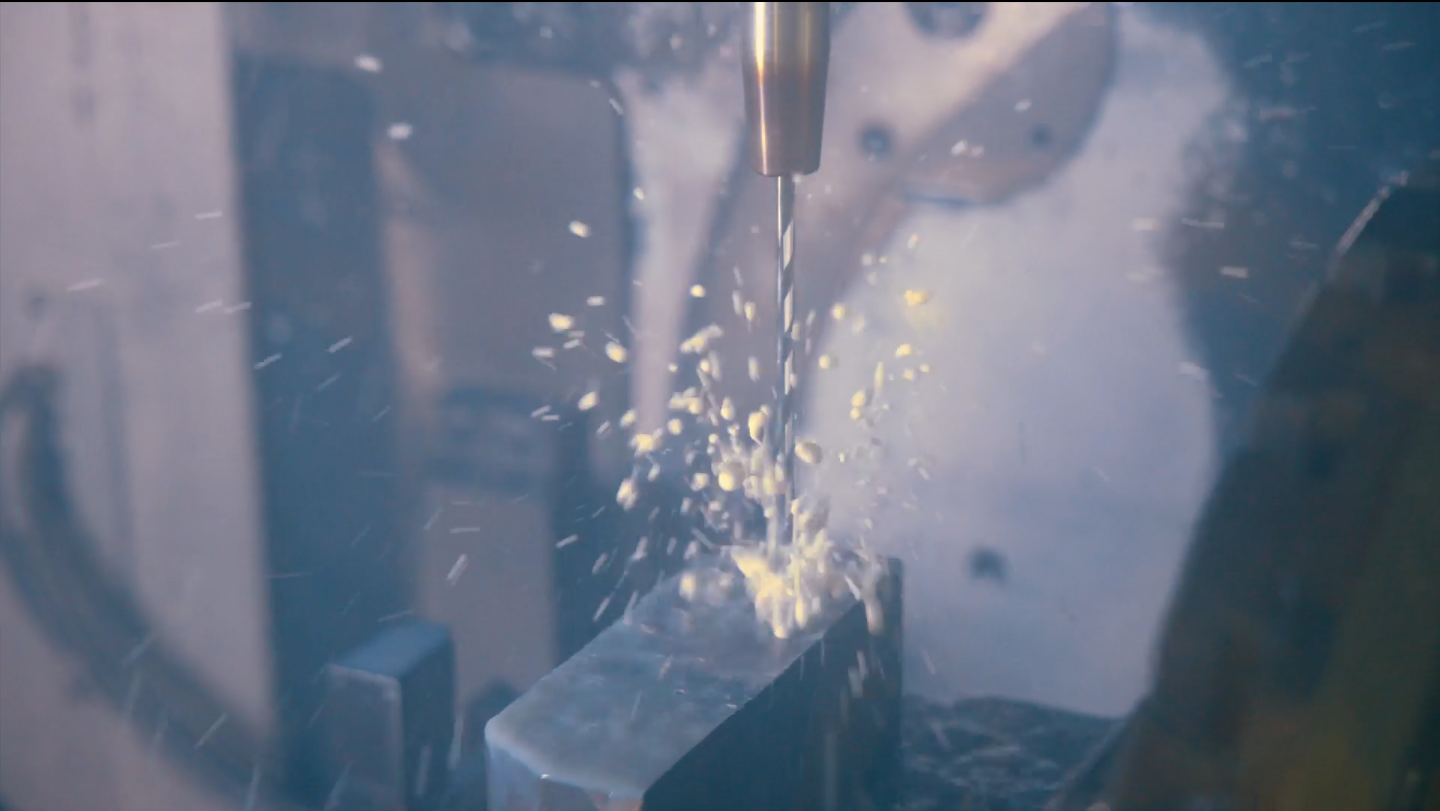
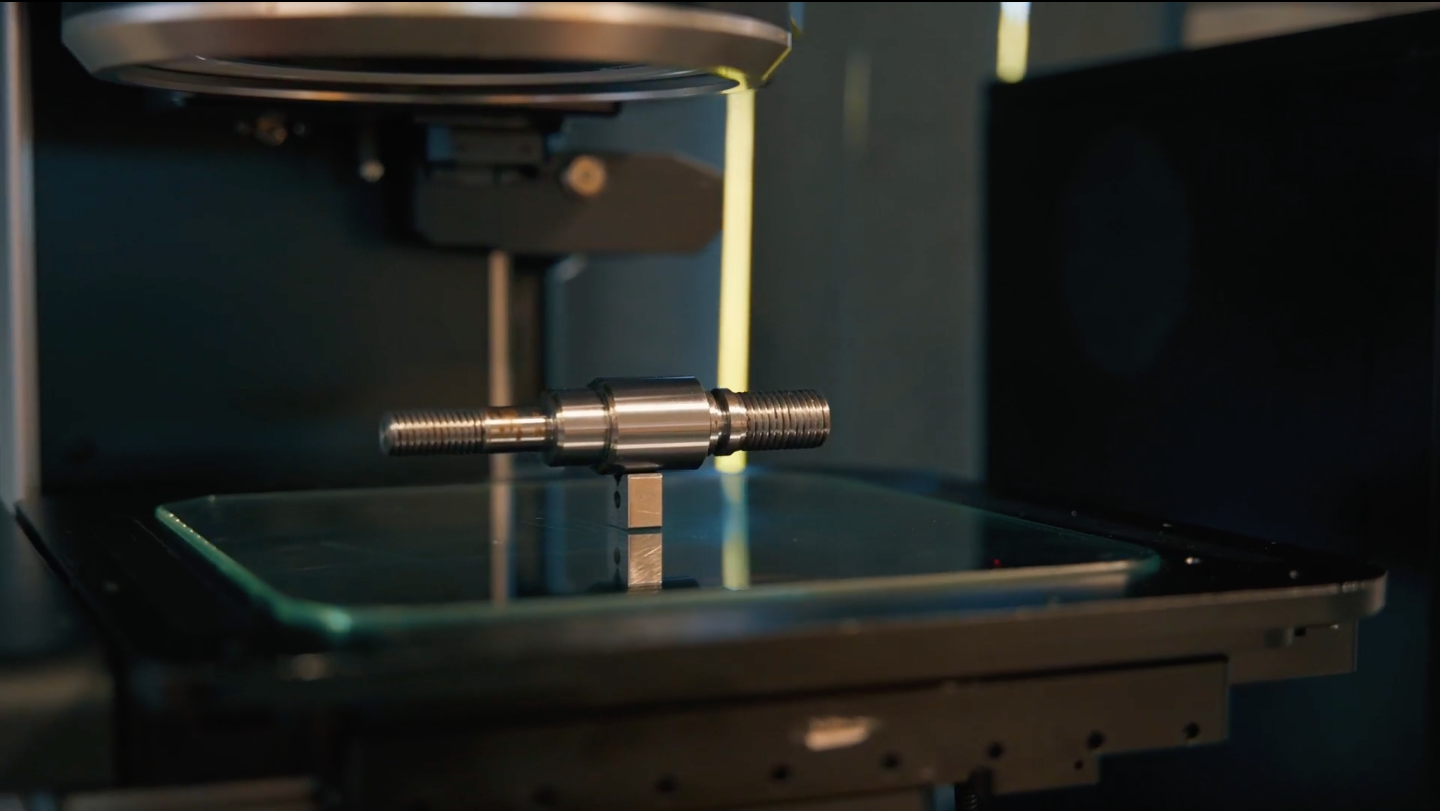