~ All You Need to Know About CNC Machining Services ~
CNC machining not only accelerates production but also ensures consistently high-quality output.
In the realm of modern manufacturing, CNC machining has been established as a cornerstone technology. Its unparalleled precision, speed, and versatility have revolutionised industries ranging from aerospace and automotive to healthcare and electronics. CNC machining not only accelerates production but also ensures consistently high-quality output, making it a vital tool for meeting the demands of today's competitive markets.
If you are interested in exploring the topic of CNC machining services, you have come to the right page! In this article, we cover everything from the fundamentals of CNC machining and its various types to its wide-ranging applications across industries. By the end, you'll have a thorough grasp of how
CNC machining services can benefit your specific manufacturing needs. But before we dive in, let's understand what CNC machining is.
What is CNC Machining?
CNC machining, short for Computer Numerical Control machining, is a cutting-edge manufacturing process that utilises computerised systems to control and operate precision machining tools. It represents a significant leap in automation and precision compared to traditional manual machining methods. By using computer-generated codes, CNC machines can produce intricate and highly accurate parts and components for various industries.
At its core, CNC machining involves the use of pre-programmed computer software to dictate the movements of machining tools and equipment. This precise control enables the creation of complex shapes, intricate designs, and highly accurate measurements that would be otherwise unattainable through manual machining. CNC machines can perform a wide array of operations, including cutting, drilling, milling, and turning, with exceptional speed and consistency.
The roots of CNC machining trace back to the mid-20th century, with the development of early numerical control systems. Over the decades, advancements in computing power, software engineering, and mechanical engineering have propelled CNC technology forward. Today's CNC machines are equipped with sophisticated software, high-speed spindles, and multi-axis capabilities, allowing for an unprecedented level of precision and complexity in manufacturing.
Types of CNC Machines
There are several types of CNC machines, each designed for specific machining tasks. Common examples include CNC milling machines, which remove material from a workpiece using rotating cutters, and CNC lathes, which use turning tools to shape materials. CNC routers are specialised for intricate cuts in wood, plastics, and composites, while CNC grinders are used for precision surface finishing.
How Do CNC Machines Work?
CNC machines rely on a combination of hardware and software components to execute machining operations. The heart of the system is the CNC controller, which interprets digital instructions and converts them into precise movements of the machine's tools. The controller communicates with motors that drive the motion of the machine along multiple axes. Additionally, sensors and feedback systems ensure real-time adjustments for accuracy.
Materials Used in CNC Machining
Metals (Aluminum, Steel, Titanium, etc.)
CNC machining is well-suited for a wide range of metals. Aluminum, known for its lightweight yet durable properties, is a popular choice for aerospace and automotive applications. Steel, with its exceptional strength, is widely used in engineering and manufacturing. Titanium, prized for its high strength-to-weight ratio, finds applications in aerospace and medical implants.
Plastics and Polymers
CNC machining is highly adaptable to plastics and polymers, making it an excellent choice for industries like electronics and medical devices. Materials such as ABS, acrylics, and PEEK can be precisely machined to create custom components. The versatility of CNC machining allows for intricate designs and complex shapes in plastic materials.
Composites
Composite materials, which combine different materials for enhanced properties, are increasingly used in aerospace, automotive, and sports industries. CNC machining is capable of accurately shaping and finishing composite components. This is crucial for maintaining the structural integrity and performance of composite materials.
Wood and Other Natural Materials
CNC machining extends its capabilities to natural materials like wood. This is especially relevant in industries such as furniture manufacturing and architectural detailing. CNC routers can intricately carve and shape wood, allowing for detailed designs and precise joinery. The versatility of CNC machining enables it to work with a wide range of natural materials.
Applications of CNC Machining
Aerospace Industry
The aerospace sector relies heavily on CNC machining for the production of critical components. From intricate engine parts to structural elements, CNC machining ensures the precision and reliability required for safe and efficient flight. The ability to work with high-strength materials like titanium and nickel alloys makes CNC machining indispensable in aerospace manufacturing.
Automotive Industry
In the automotive industry, CNC machining plays a pivotal role in the production of engine components, transmission parts, and intricate chassis elements. The precision of CNC machines ensures that these critical components meet strict performance and safety standards. Additionally, CNC machining allows for the customisation of components for specialised vehicles or prototypes.
Medical and Dental Industries
CNC machining is vital in the production of medical implants, prosthetics, and various surgical instruments. The high level of precision and biocompatible materials compatibility make it a preferred choice. CNC technology also enables the rapid prototyping of medical devices, allowing for iterative design improvements before final production.
Electronics and Technology Sector
The electronics industry benefits greatly from CNC machining for creating customised enclosures, connectors, and heat sinks. The precision and consistency of CNC machines are crucial for ensuring that electronic components fit seamlessly within devices. Additionally, the ability to work with various materials allows for versatility in product design and functionality.
Custom Prototyping and Small-Scale Production
CNC machining is invaluable for rapid prototyping and small-scale production runs. It allows for the creation of prototypes that closely mirror the final product, enabling thorough testing and validation. This accelerates the product development cycle and facilitates quick adjustments based on feedback. Small-scale production runs benefit from the cost-effectiveness and high precision of CNC machining.
How Do Manufacturers Benefit from CNC Machining Services?
Precision and Accuracy
One of the most significant advantages of CNC machining is its unrivalled precision. The ability to program exact specifications ensures that each component produced meets tight tolerances. This level of accuracy is crucial in industries where even the slightest deviation can lead to product failure.
High Production Capacity
CNC machining excels in high-volume production runs. With automated processes and rapid tool changes, CNC machines can churn out large quantities of parts with remarkable efficiency. This capability significantly reduces lead times and allows for the timely delivery of products to meet market demands.
Versatility in Material Compatibility
CNC machining is not limited to a single type of material. Whether working with metals like aluminium, steel, or titanium, or processing plastics, composites, or wood, CNC machines are adaptable to a wide range of materials. This versatility makes them invaluable in industries with diverse material requirements.
Complex Geometries and Intricate Designs
Thanks to their programmable nature, CNC machines excel at producing parts with intricate and complex geometries. From fine details to 3D contours, CNC machining can accurately replicate even the most intricate designs. This capability is particularly crucial in industries like aerospace and medicine, where intricate components are commonplace.
Cost-Effectiveness in Large Productions
While CNC machining offers high precision and versatility, it also delivers cost-effectiveness in large-scale production runs. The automation of processes reduces the need for manual labour, minimises material waste, and ensures consistent quality. These factors combine to provide a cost-effective solution for mass production.
What Do CNC Machining Services Include?
CNC machining services encompass a range of processes and capabilities that utilise Computer Numerical Control (CNC) technology to manufacture precise and intricate components. These services typically include:
Milling
CNC Milling is a fundamental CNC machining process where a rotating cutting tool removes material from a workpiece to achieve the desired shape or form. It is suitable for creating flat surfaces, pockets, slots, and complex 3D profiles. CNC milling machines come in various configurations, including vertical, horizontal, and multi-axis, allowing for versatility in machining operations.
Turning
Turning is the process of rotating a workpiece on a lathe while a stationary cutting tool shapes it. This process is ideal for creating cylindrical components, such as shafts, pins, and bushings. CNC lathes can perform both external and internal turning operations, producing precise and concentric parts.
Drilling
CNC drilling involves creating holes in a workpiece using a rotating tool. This process is crucial for various industries, including aerospace, where precise hole placement is vital for assembly. CNC drilling machines are equipped with high-speed spindles and automatic tool changers for efficient hole production.
Grinding
Grinding is a precision machining process used to achieve tight tolerances and exceptional surface finishes. It involves removing material from a workpiece using abrasives. CNC grinding machines are employed for applications that require extreme precision, such as in the production of bearings, gears, and tooling components.
Electrical Discharge Machining (EDM)
EDM is a non-traditional machining process that utilises electrical discharges to erode material from a workpiece. It is highly effective for machining complex shapes in hard materials like tool steel or exotic alloys. CNC EDM machines use precise control over electrical discharges to achieve accurate and intricate details.
Laser Cutting
Laser cutting utilises a high-powered laser beam to precisely cut through materials. CNC laser cutting machines are capable of handling a wide range of materials, including metals, plastics, and composites. This process is known for its speed and accuracy, making it a preferred choice for industries that require intricate and detailed cuts.
Programming and Software
CNC machining services also include the use of Computer-Aided Design (CAD) and Computer-Aided Manufacturing (CAM) software to create and program toolkits for machining operations.
Quality Assurance and Inspection
This involves a range of techniques, including the use of Coordinate Measuring Machines (CMM), optical comparators, and surface roughness testers, to ensure that the final components meet specified tolerances and quality standards.
Material Compatibility
CNC machining services encompass working with various materials, including metals (like aluminium, steel, and titanium), plastics, composites, and natural materials.
Custom Prototyping
Many CNC machining service providers offer rapid prototyping services, allowing for the creation of prototypes that closely resemble the final product for testing and validation.
Small-Scale Production
CNC machining services can be utilised for small-scale production runs, providing a cost-effective solution for producing precise components.
Final Thoughts
As you consider your manufacturing needs, remember that CNC machining services offer a level of precision, versatility, and efficiency that is unmatched by traditional machining methods. Whether you're in aerospace, automotive, medical, or any other industry, CNC machining can be a transformative tool in your production process.
If you're ready to experience the transformative power of CNC machining for your manufacturing needs, look no further than Rotec. With a proven track record of precision, quality, and expertise, we can bring your designs to life with unparalleled accuracy.
Contact us today and discover how Rotec's CNC machining services can elevate your production capabilities to new heights!
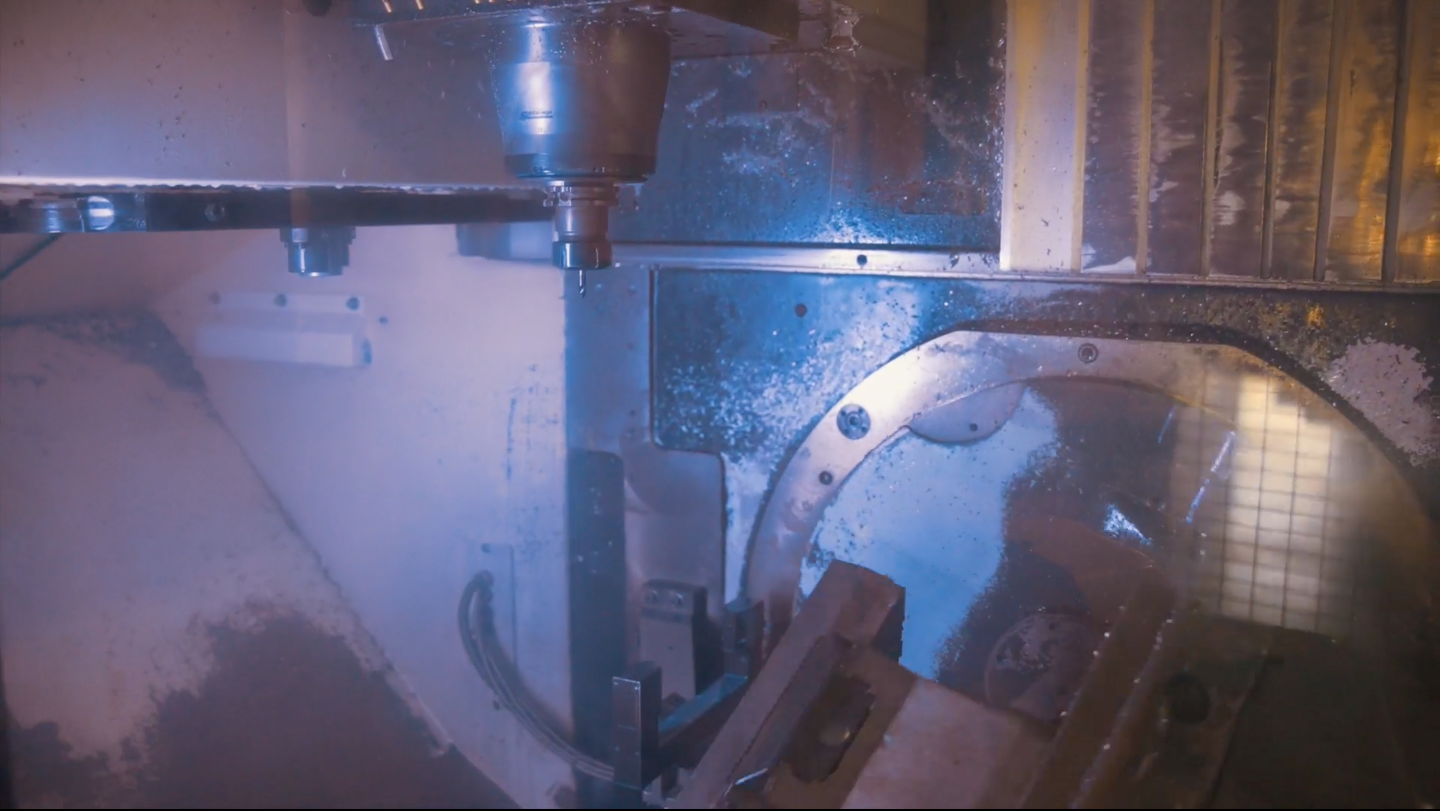
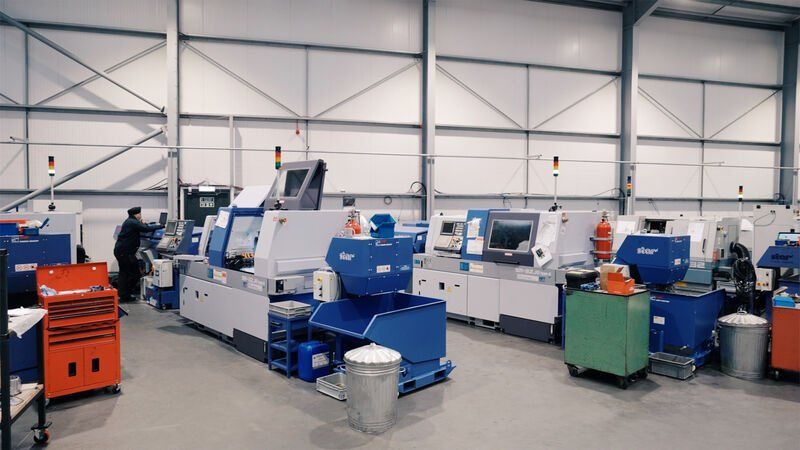
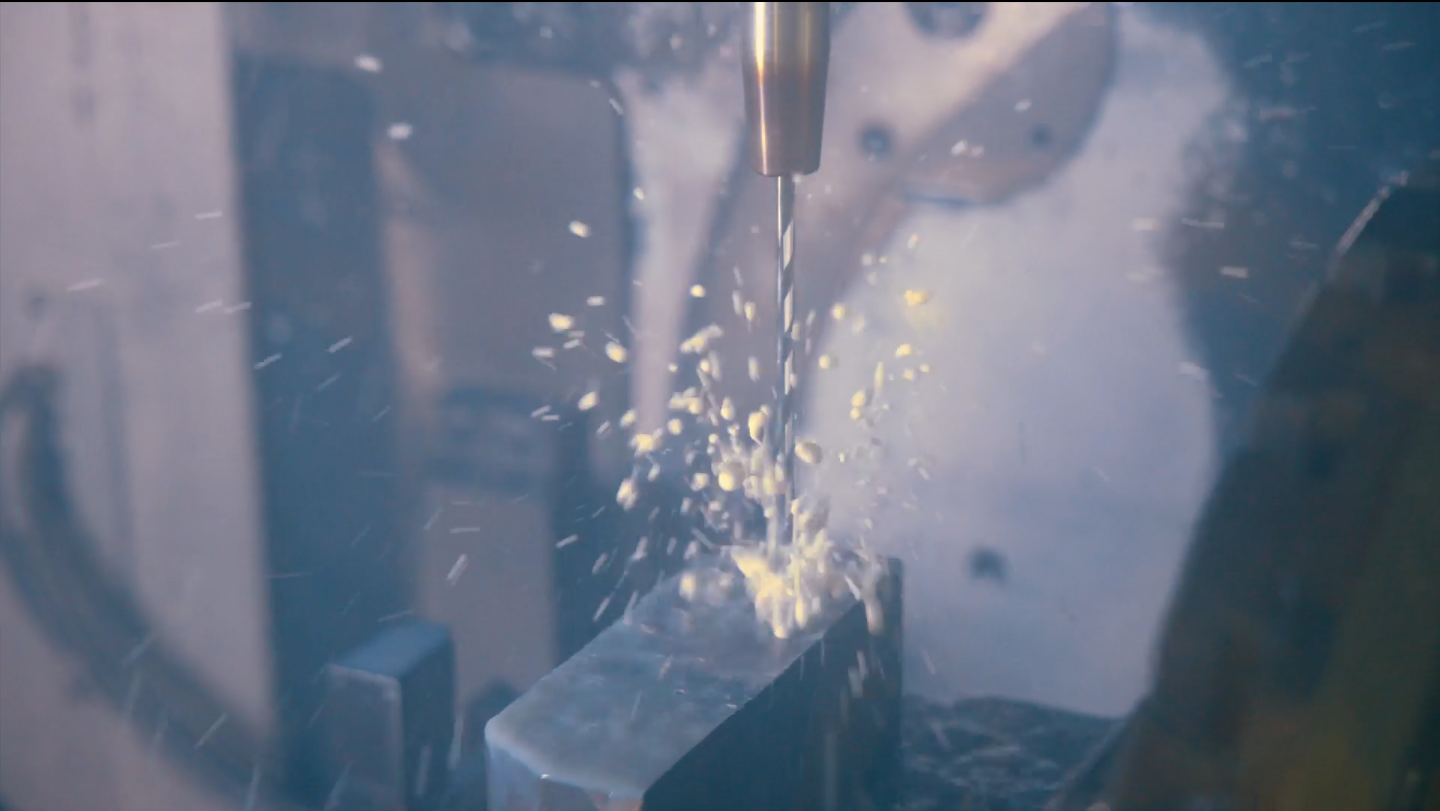
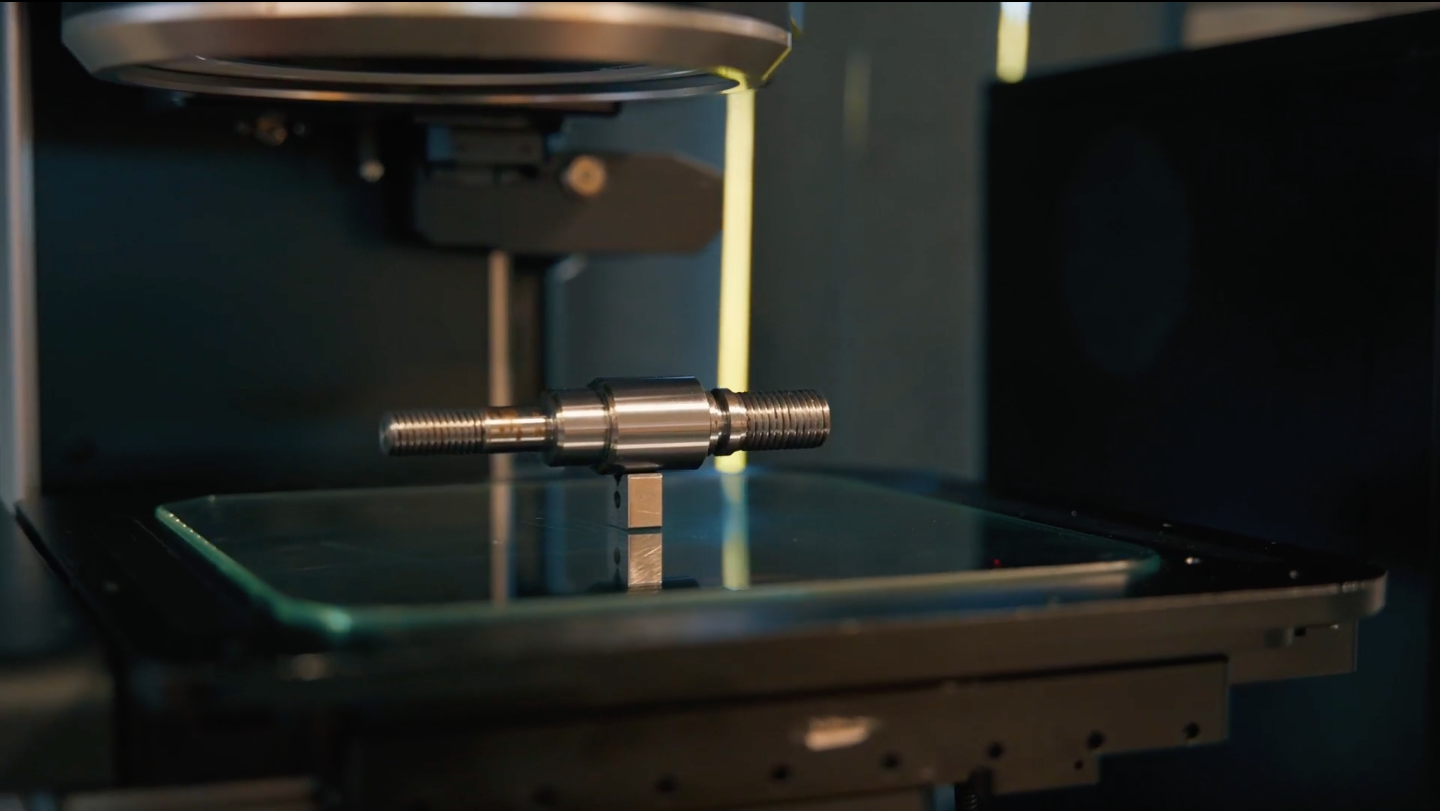