~ Can CNC Plasma Cutters Work With Aluminium? ~
The demand for intricate designs using lightweight and versatile Aluminum prompts the question: Can CNC plasma cutters handle it?
In the ever-evolving landscape of metal fabrication and precision engineering, the synergy between cutting-edge technology and the intrinsic qualities of materials has reshaped the possibilities within industries such as aerospace, automotive, and beyond. As the spotlight turns toward Aluminium, a metal renowned for its light weight and versatility, there's a growing demand for intricate and complex designs using this material. No wonder why many seek answers to this crucial question: Can CNC plasma cutters effectively handle Aluminium?
If you are wondering the same, you have come to the right page! In this article, we will share the nuances of CNC plasma cutting, examining its compatibility with Aluminium, exploring the advantages and challenges of
aluminium cutting, and envisioning the future of precision engineering. Let's dive right in!
Understanding CNC Plasma Cutting
CNC technology has become synonymous with precision and automation in the manufacturing world. In the realm of metal cutting, CNC plasma cutting stands out for its ability to slice through various materials with unparalleled accuracy. Utilising a combination of numerical control and a high-velocity jet of ionised gas, CNC plasma cutters are capable of creating intricate shapes and designs.
The process involves a computerised system interpreting design specifications and translating them into precise movements of the plasma torch. This level of automation not only enhances the accuracy of cuts but also allows for the creation of intricate patterns that would be challenging with traditional cutting methods.
Characteristics of Aluminium
Before delving into the compatibility of CNC plasma cutting with Aluminium, it's essential to understand the unique characteristics of this metal. Aluminium is known for its excellent strength-to-weight ratio, corrosion resistance, and thermal conductivity. However, these very characteristics present challenges when it comes to traditional cutting methods.
The lightweight nature of Aluminium can make it susceptible to warping or distortion from excessive heat during cutting. Additionally, its high thermal conductivity requires a cutting method that can efficiently manage heat. CNC plasma cutting, with its controlled and focused application of heat, emerges as a potential solution to these challenges.
Plasma Cutting vs Laser Cutting: Which One is Better for Aluminium?
When it comes to cutting Aluminium sheets, fabricators often debate between plasma cutting and laser cutting. These are two different methods used in metal fabrication, each with its own strengths and weaknesses. In this article, we'll focus on comparing plasma cutting and laser cutting specifically for Aluminium sheet fabrication.
Cutting Range
Plasma cutters can only cut materials that conduct electricity, limiting them to metals. On the other hand, laser cutters can work on various materials with high precision. In terms of cutting range and material thickness, plasma cutting outperforms laser cutting. Plasma cutting can handle Aluminium sheets and plates up to 38mm in thickness, whereas laser cutting is limited to 12.7mm.
Precision
The precision of both methods depends on the thickness of the Aluminium. For thin sheets, sheet metal laser cutting provides a more precise cut, creating narrow slots with high accuracy, often less than 0.01mm. In contrast, plasma cuts have a larger slot with precision ranging between 0.5-1mm. However, it's worth noting that laser cutting's precision decreases significantly as the material thickness increases, while plasma cutting maintains higher precision when working with thick Aluminium sheets.
Productivity
Productivity varies based on the thickness of the Aluminium or other metals being cut. Laser cutting is more productive for thinner metals due to its speed, but its productivity decreases significantly with thicker materials. Plasma cutting, on the other hand, maintains better productivity with an increase in thickness.
Operation Cost
Beyond the initial investment, laser cutting machines also incur higher operational costs. On average, the operating cost for laser cutters is more than that of plasma cutters. This cost includes expenses for power, gases, maintenance, and replacing worn-out parts.
Equipment Cost
Investing in a laser cutter is a more expensive endeavour compared to purchasing a plasma cutter. The capital cost for laser cutters varies a lot, depending on the features you need, while you can acquire a plasma cutter for a much cheaper price.
In conclusion, the choice between plasma cutting and laser cutting for Aluminium fabrication depends on factors such as precision requirements, cutting range, equipment and operation costs, and the thickness of the material. Understanding these aspects will help you make an informed decision based on your specific needs and budget constraints.
Compatibility of CNC Plasma Cutters with Aluminium
CNC plasma cutting technology has evolved to handle a diverse range of materials, including Aluminium. The compatibility of CNC plasma cutting with Aluminium hinges on several factors. The type of CNC plasma cutter used plays a crucial role, as different machines come with varying power levels and capabilities.
When it comes to Aluminium cutting, the key is to fine-tune parameters such as cutting speed, gas flow, and torch height to accommodate the metal's unique properties. CNC plasma cutters equipped with advanced systems can effectively navigate through varying thicknesses of Aluminium, ensuring precision and consistency in the cutting process.
Advantages of CNC Plasma Cutting for Aluminium
CNC plasma cutting offers several advantages when it comes to working with Aluminium:
Precision and Accuracy: The CNC system's ability to interpret complex designs results in precise and accurate cuts, maintaining tight tolerances even on intricate patterns.
Versatility: Aluminium often requires cutting into complex shapes, and CNC plasma cutting excels in this regard. Its versatility allows for the creation of custom designs with ease.
Cost-Effectiveness: CNC plasma cutting proves to be a cost-effective solution for Aluminium cutting, especially when compared to laser cutting or water jet cutting methods. It strikes a balance between efficiency and affordability.
Challenges and Considerations
While CNC plasma cutting offers numerous benefits for Aluminium, it's essential to address potential challenges:
Thermal Considerations: Aluminium's high thermal conductivity can lead to heat-affected zones and potential distortion. Proper parameter settings and the use of advanced CNC systems can help mitigate these issues.
Edge Quality: Achieving a smooth edge finish is crucial in many applications. CNC plasma cutting may require additional post-processing steps to refine the cut edges for specific requirements.
Maintenance: Regular maintenance of CNC plasma cutters is essential to ensure optimal performance. This includes checking and replacing consumables, inspecting the torch, and monitoring the overall system for wear and tear.
Plasma Cutting Aluminium: A Quick Guide
Plasma cutting Aluminium is similar to cutting steel, but differences in gas, nozzle, and settings are crucial. Here's a simplified breakdown:
1. Gas Selection
Using regular air can result in rough cuts due to oxidation. Optimal gas mixtures vary:
- For Aluminium over half an inch thick: Primary - argon-helium, Secondary - nitrogen.
- For Aluminium under half an inch thick: Primary - nitrogen, Secondary - compressed air.
2. Nozzle Importance:
Nozzles made from copper alloy work best, conducting heat and electricity effectively.- Nozzle size affects cut angle, power, and size. Choose smaller orifices for larger arcs and higher voltages.
- Check the temperature limit on the nozzle to prevent melting or reduced lifespan.
3. Machine Settings:
Consult your machine manual for accurate settings, including amperage and torch speed for Aluminium cutting.- Cutting speed is crucial; too slow wastes power, while too fast may lead to unsuccessful cuts.
- Generally, cutting speeds range from 1695 mm/m to 4750mm/m, depending on arc voltage and Aluminium thickness.
Plasma cutting is an effective method for fabricating Aluminium parts, but success requires technical knowledge, skill, and the right equipment.
Reducing Risks in Aluminium Plasma Cutting
Use a Tank with Water Level Control
Lowering the water level helps release hydrogen molecules, reducing the risk of explosions.
Wear Protective Gear
Utilise a welding helmet, goggles, gloves, boots, jackets, earmuffs, and chaps to protect against sparks and radiation during plasma cutting.
Protect Eyes from UV Radiation
Wear goggles to prevent cornea burns from ultraviolet radiation generated during cutting (arc eye).
Install an Aerator
Setup with tubes releases air bubbles under the Aluminium, pushing hydrogen away and decreasing the risk of explosions.
Use a Bubble Muffler
Device shields plasma, using compressed air to eliminate hydrogen and direct Aluminium pieces away from the arc. Reduces UV radiation, noise, and fumes.
Install a Filtration System
Consists of a centrifuge and a high-volume pump to separate hydrogen early, preventing bubble formation. Also filters out contaminants from the water.
Avoid Unsuitable Aluminium Alloys
- Anodized Aluminium: Vulnerable to high temperatures, damaging the metal surface during plasma cutting.
- Aluminium Floor Plate: Raised sections interfere with the plasma cutter's control and result in poor cut quality.
- Aluminium-Lithium Alloys: High volatility around water; cutting in water can lead to explosions or flames.
Immediate Removal of Aluminium Pieces in Water
If Aluminium pieces fall into the water during cutting, remove them promptly to prevent potential hazards.
By following these safety measures and precautions, the risks associated with hydrogen explosions and other hazards during Aluminium plasma cutting can be significantly minimised. Always prioritise safety and choose appropriate materials to ensure a secure and efficient cutting process.
Tips for Optimising CNC Plasma Cutting of Aluminium
To maximise the benefits of CNC plasma cutting when working with Aluminium, consider the following tips:
Setting the Right Parameters: Fine-tuning the cutting parameters is crucial. Adjust factors such as cutting speed, amperage, and gas flow to accommodate the specific characteristics of Aluminium and the thickness of the material.
Choosing the Appropriate Apparatus: Selecting the right apparatus, including nozzles and electrodes, is essential for achieving clean cuts. Specialised apparatus designed for Aluminium cutting can enhance performance and extend the life of the cutting components.
Regular Maintenance and Troubleshooting: Consistent maintenance is key to the longevity and efficiency of CNC plasma cutters. Regularly inspect consumables, check for wear, and perform routine maintenance to address any issues promptly.
Future Trends and Innovations
The world of CNC plasma cutting is ever-evolving, with ongoing research and development aiming to enhance the capabilities of these systems. When it comes to
cutting Aluminium, future trends and innovations may include:
Advanced CNC Systems: Continuous advancements in CNC technology will likely result in more sophisticated systems with improved automation, allowing for even greater precision in Aluminium cutting.
Enhanced Cooling Systems: Innovations in cooling mechanisms may address the thermal challenges posed by Aluminium, ensuring optimal cutting conditions without compromising material integrity.
Integration with Advanced CAD/CAM Software: The integration of CNC plasma cutting systems with advanced CAD/CAM software has the potential to optimise the design-to-cutting process, further enhancing efficiency and accuracy.
Final Thoughts
The compatibility of CNC plasma cutters with Aluminium is not only feasible but also offers numerous advantages. The precision, versatility, and cost-effectiveness of CNC plasma cutting make it a compelling choice for various industries requiring Aluminium components with intricate designs. As CNC plasma cutting continues to evolve, we can expect even more efficient and effective solutions for Aluminium cutting in the future.
If you're looking to start on projects that demand the utmost precision and expertise in CNC machining and plasma cutting, look no further than Rotec. With a proven track record in handling complex CNC machining projects, our precision engineering team is ready to bring your visions to life. To explore the possibilities,
contact us today!
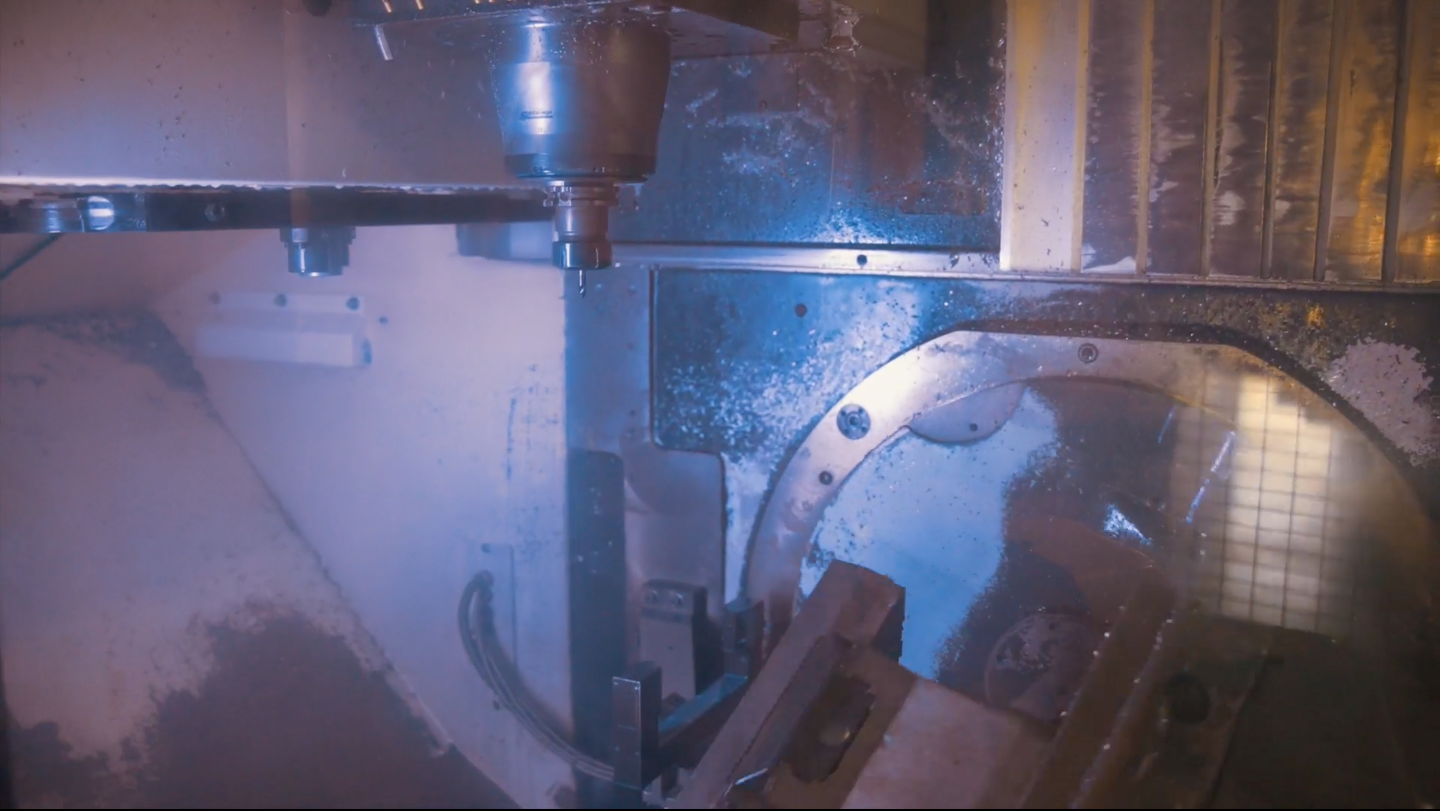
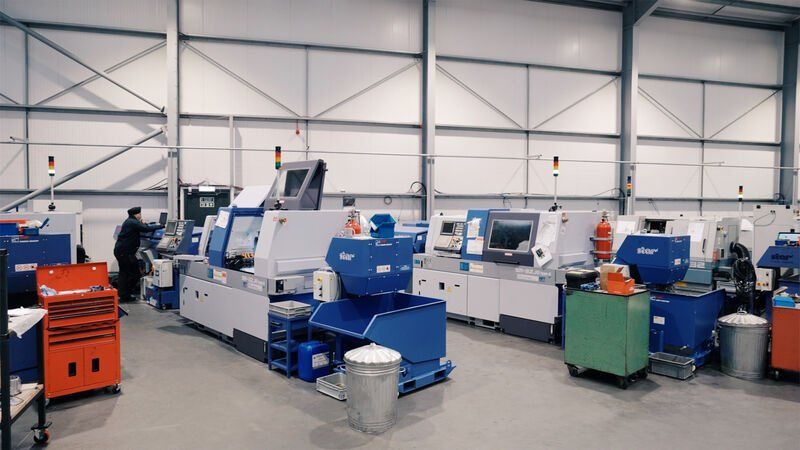
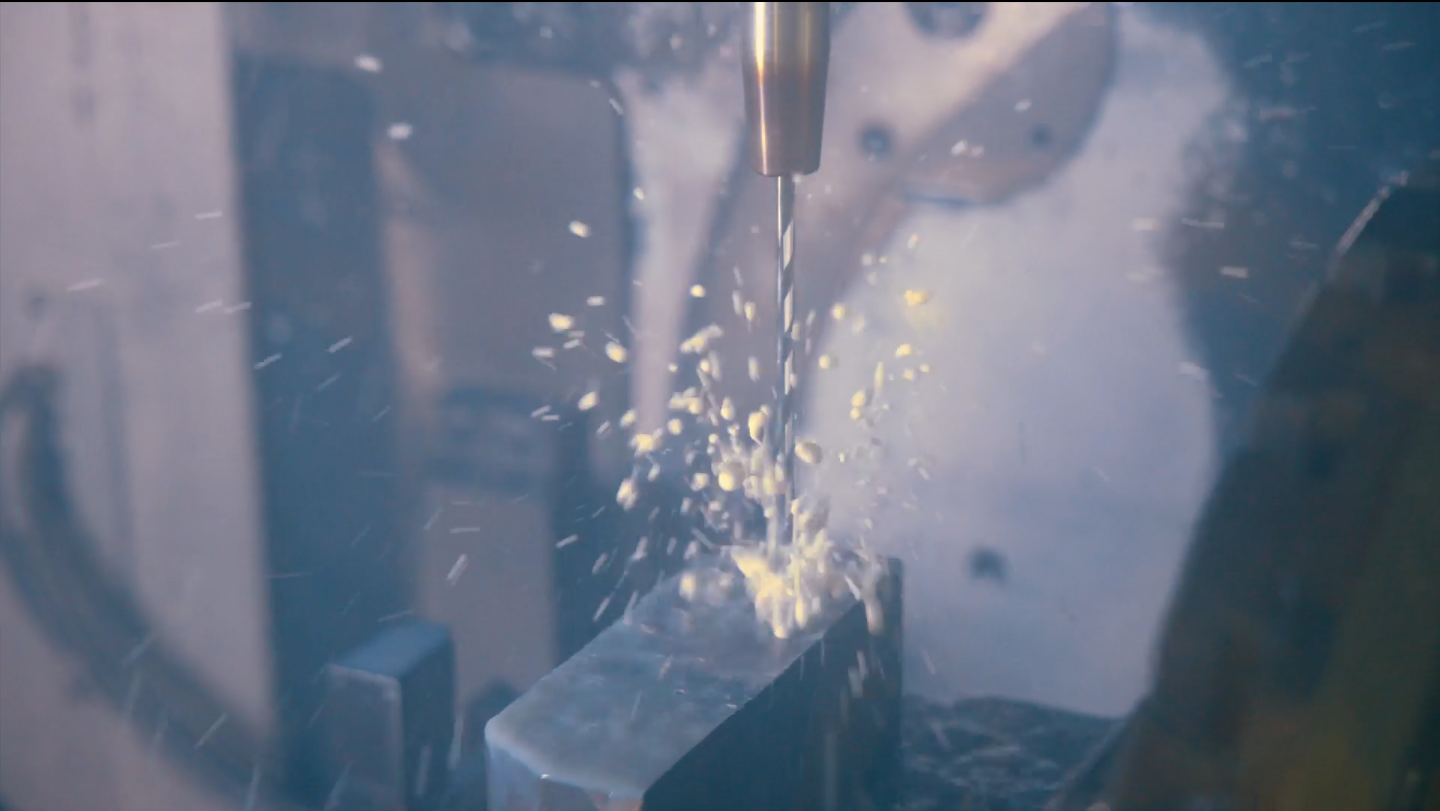
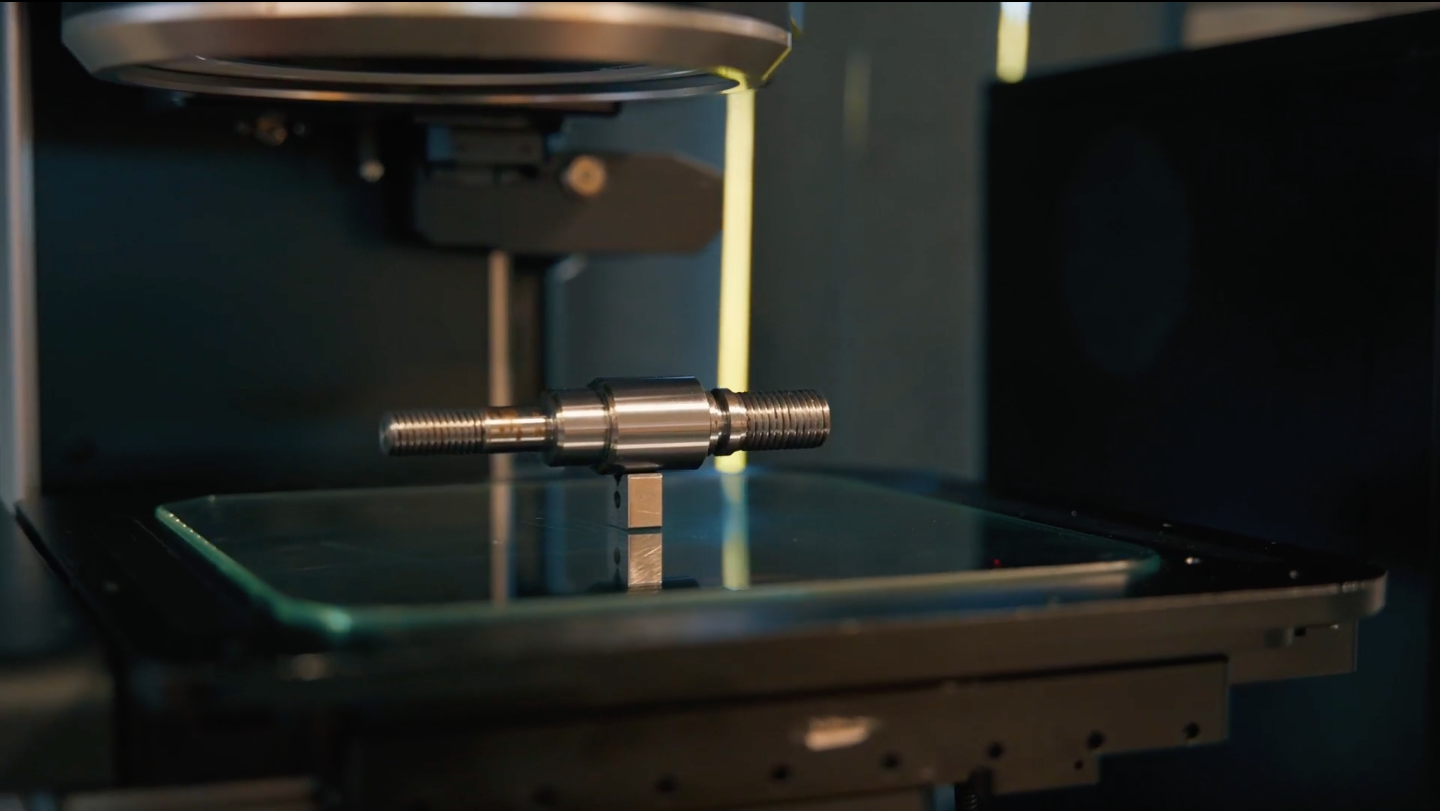